Gas or electric, batch or continuous – the options are well known to forging manufacturers, but the question lingers: is there an ideal heating technology for forging production. The answer, of course, depends on the material to be forged, and even more so on the forging operation.
Lake City Forge in Lake City, MI, is operating a new, 1,000-kW induction heating system for forging billets developed and installed by Ajax Tocco Magnethermic Corp. The closed-die forging operation processes carbon and alloy steel into products like pitman arms, upper control arms, driveline yokes, marine yokes, steering arm, lateral links, tension links, connecting rods, and shift forks for automotive, light and commercial truck, agricultural equipment, and mining sectors.
The TS16949- and ISO14001-certified plant operates three 6,000-lb CECO drop hammer machines and two Lasco programmable hammer machines, as well as four cross-wedge rolling machines. The variety of operations and products manufactured there were indicators that induction heating was the right technology selection. It is fast and flexible enough to allow adjusting heating schedules to forging production schedules.
Ajax TOCCO’s 1,000-kW, 1.3- to 3.3-kHz PowerZone billet-heating system heats 1.06- to 2.875-in. diameter x 6.0- to 20.0-in. long, carbon steel billets to forging temperatures. The system is capable of changing frequency automatically for differing billet sizes, and operators will access the custom ForgeView Plus operating software via a touchscreen-display PLC system.
For Lake City Forge, the new system will be loaded with billets by a vibratory bowl feeder.
According to Ajax, parent company LC Manufacturing selected the system due its comprehensive operating capability; the availability of the multi-frequency PowerZone functions, in order to run a wide variety of parts; the availability of maintenance services, when necessary; and its own prior experience with Ajax induction heating systems.
But a new forging operation in development across the country has different process requirements: high-volume throughput of large-dimension titanium and aluminum billets.
Can-Eng Furnaces International Ltd. is designing a rotary hearth furnace to heat titanium and alloy billets for Weber Metals Inc., Paramount, CA. The furnace installation is part of the $170-million capital investment centering on a new closed-die press that will forge extra-large nickel- and titanium-based alloy parts for commercial aerospace contracts, including Airbus and Boeing projects.
Rotary hearth furnaces are continuous operations in which charge material is conveyed directly over the furnace hearth on a turntable inside the heating chamber, powered by an external drive. They are considered to be a very reliable and sturdy way to heat multiple billet and/or bloom sizes. They are often designed as the central element of a continuous heating process, with programmable heating and automated billet handling
Weber Metals is a subsidiary of Germany’s Otto Fuchs KG, producing open-die and closed-die forgings in aluminum and titanium alloys, mainly for aerospace manufacturing, like aircraft fuselage and wing structures, as well as landing gears. Presently, the plant operates four open-die presses (rated at 1,200 to 5,000 tons) and five closed-die machines (rated at 1,500 to 33,000 tons.)
But, the new rotary hearth furnace is not the only heating requirement for Weber Metals, nor the only assignment for Can-Eng Furnaces. It will design, manufacture, and commission a conveyor forging furnace for aluminum billets at the California plant. The automated heating chamber will raise aluminum alloy preforms and billets to forging temperature.
Can-Eng Furnaces develops industrial furnaces not only for heating but also for various heat treating processes (sintering, clean hardening, light case carburizing and carbonitriding, austempering, and martempering), for steel and aluminum.
The Weber Metals project centers on a new, 60,000-ton press designed by SMS and described as “the largest aerospace forging press in the Western Hemisphere, and the largest in the world installed with private investment.” Start-up is planned for late 2017.
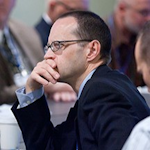
Robert Brooks | Editor/Content Director - Endeavor Business Media
Robert Brooks has been a business-to-business reporter, writer, editor, and columnist for more than 20 years, specializing in the primary metal and basic manufacturing industries. His work has covered a wide range of topics including process technology, resource development, material selection, product design, workforce development, and industrial market strategies, among others.
Currently, he specializes in subjects related to metal component and product design, development, and manufacturing—including castings, forgings, machined parts, and fabrications.
Brooks is a graduate of Kenyon College (B.A. English, Political Science) and Emory University (M.A. English.)