Otto Fuchs KG has ordered a new, SMS closed-die forging press for its Weber Metals subsidiary in Paramount, CA, near. Los Angeles. The new machine, planning for which has been underway for several years, will forge extra-large nickel- and titanium-based alloy parts for commercial aerospace contracts, including Airbus and Boeing projects.
When Weber Metals staged a groundbreaking ceremony for the new press two years ago, it described the project as a $170-million investment. Local reports detailed that the machine would be “the largest aerospace forging press in the Western Hemisphere, and the largest in the world installed with private investment.”
According to SMS, its GUF4-type hydraulic press will be a "pit mounted" design capable of achieving forces of 540 MN (60,000 tons/in.2), with a 6,000X3,000-mm (236X118 in.) die clamping area and a stroke of 2,000 mm (79 in.)
SMS noted that steel castings produced for the four-column press will weigh up to 350 mt (386 tons.) The new machine will be structurally reinforced with four, forged tie rods, an integrated load-balancing feature that will allow the operators to forge parts to extremely tight tolerances.
Start-up for the new press is expected late in 2017.
“This large-scale investment underpins our strategic alignment in the global aerospace market,” stated Dr. Klaus Welschof, aerospace industry sales manager for Otto Fuchs.
Weber Metals has been a subsidiary of Otto Fuchs since 1978, producing open-die and closed-die forging in aluminum and titanium alloys, mainly for aerospace manufacturing, like aircraft fuselage and wing structures, as well as landing gears.
Presently, the plant operates four open-die presses (rated at 1,200 to 5,000 tons) and five closed-die machines (rated at 1,500 to 33,000 tons.)
SMS noted the new press would allow Otto Fuchs to expand its portfolio of “extra-large premium-grade forgings” into even larger dimensions, and introduce the possibility of converting large structural components to lighter materials.
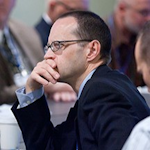
Robert Brooks | Editor/Content Director - Endeavor Business Media
Robert Brooks has been a business-to-business reporter, writer, editor, and columnist for more than 20 years, specializing in the primary metal and basic manufacturing industries. His work has covered a wide range of topics including process technology, resource development, material selection, product design, workforce development, and industrial market strategies, among others.
Currently, he specializes in subjects related to metal component and product design, development, and manufacturing—including castings, forgings, machined parts, and fabrications.
Brooks is a graduate of Kenyon College (B.A. English, Political Science) and Emory University (M.A. English.)