Continuous Improvement Needs to Be Embedded into Work Flow of Plant
This natural tendency to deprioritize improvement work represents a significant challenge but fortunately not an insurmountable one. What is required is a systematic approach that embeds improvement activities into the work flow of the plant so that they are routinized in a manner similar to the “operate and maintain” activities.
The most important paradigm shift that needs to occur to successfully embed CI into the DNA of the organization is to change people’s mental model such that they stop thinking of improvement work as a series of largely disjointed or unrelated activities competing for increasingly limited time and resources.
The approach for enabling this paradigm shift can’t be to introduce new CI methodologies (e.g., lean, Six Sigma, TPM, etc.) or tools (kaizens, SMED, kanbans, etc.) into the organization because, as described previously, the lack of priority for CI has little to do with the methodology or tools and a lot to do with the perception that improvement work is of secondary importance or otherwise distracts from more urgent operational matters.
More on continuous improvement on IndustryWeek.
IndustryWeek is an NED companion site within Penton’s Manufacturing & Supply Chain Group.
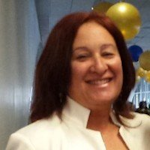
Adrienne Selko | Senior Editor - MH&L, IW, & EHS Today
Adrienne Selko has written about many topics over the 17 years she has been with Endeavor Business Media and currently focuses on workforce development strategies. Previously Adrienne was in corporate communications at a medical manufacturing company as well as a large regional bank.
She is the author of Do I Have to Wear Garlic Around My Neck? which made the Cleveland Plain Dealer's best sellers list. She is a senior editor at Material Handling & Logistics, EHS Today, and IndustryWeek.
Editorial Mission Statement:
Manufacturing is the enviable position of creating products, processes, and policies that solve the world’s problems. When the industry stepped up to manufacture what was necessary to combat the pandemic, it revealed its true nature. My goal is to showcase the sector’s ability to address a broad range of workforce issues including technology, training, diversity & inclusion, with a goal of enticing future generations to join this amazing sector.
Why I Find Manufacturing Interesting:
On my first day working for a company that made medical equipment such as MRIs, I toured the plant floor. On every wall was a photo of a person, mostly children. I asked my supervisor why this was the case and he said that the work we do at this company has saved these people’s lives. “We never forget how important our work is and everyone’s contribution to that.” From that moment on I was hooked on manufacturing.
I have talked with many people in this field who have transformed their own career development to assist others. For example, companies are hiring those with disabilities, those previously incarcerated, and other talent pools that have been underutilized. I have talked with leaders who have brought out the best in their workforce, as well as employees doing their best work while doing good for the world.