Russia’s Votkinsk Zavod is a company with more than 250 years of manufacturing history, but for now its focus is on future developments. The present organization, a “joint stock company”, is a machine-building business with in-house capabilities for melting and casting, mechanical assembly, welding, and tool-making operations as well as product testing. Recently, Votkinsk ordered a 10-MN monoframe forging press from Danieli Breda, a machine capable of forming heavy-duty specialty materials like stainless and tool steels, or high-temperature alloys used in aerospace programs.
Votkinsk Zavod (or, Votkinsk Machine Building) is one of the primary businesses of a manufacturing center established in the Volga region, about 800 miles east of Moscow. The business is known as a manufacturer of defense systems, including a number of ballistic missiles.
Last year, Votkinsk announced a capital investment program valued at nearly $100 million, to rebuild and revitalize its technical capabilities. A new forging plant is one element of the program, which also will see new metal-stamping capabilities, more modern and advanced machine tools systems, as well as new metalcasting operation to produce materials needed in defense programs, civilian infrastructure projects, and energy and aerospace engineering programs.
The capital program is schedule to be completed by December 2019.
The new operations will be centered in a new, 100,000-m2 plant, with equipment chosen and situated to achieve a rational workflow, according to Danieli Breda.
The contractor designed its open-die forging press to operate within this new concept, specifically in coordination with a rail-bound manipulator. Such design features coincide with the trend for productivity and efficiency in the development of open-die forging presses.
“The specific design of the monoframe press, which has a minimal amount of moving mass, allows smooth directional changes of the top anvil while reducing the surface temperature loss of materials that are subject to surface cracking,” according to Danieli Breda.
The new press will be able to forge high-hardness materials at speeds over 100 mm/sec., with the necessary hydraulic flow generated by a power pack comprised of 12 high-pressure piston pumps.
The motor connected power for this installation will have a rating over 1 MW.
The new press will achieve a planishing frequency of 120 strokes per minute, according to the developer, with the capacity to forge ingots weighing up to 2,000 kg. As per the future operator’s specification, the new process will be capable of completing required dimensional reductions within a single heat.
The open-die process will be controlled by the most recent iteration of the Danforge control system, for automatically programmed sequencing of forging operations. Danforge+ is a new technology platform that provides complete coordination between press and manipulators, allowing fully integrated control for high productivity and repeatability of forging cycles, as dictated by the type of material, working temperature, geometrical needs of the workpiece and dies.
Danieli Breda also will develop and supply a complete set of tools for outfitting the new open-die press.
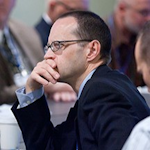
Robert Brooks | Editor/Content Director - Endeavor Business Media
Robert Brooks has been a business-to-business reporter, writer, editor, and columnist for more than 20 years, specializing in the primary metal and basic manufacturing industries. His work has covered a wide range of topics including process technology, resource development, material selection, product design, workforce development, and industrial market strategies, among others.
Currently, he specializes in subjects related to metal component and product design, development, and manufacturing—including castings, forgings, machined parts, and fabrications.
Brooks is a graduate of Kenyon College (B.A. English, Political Science) and Emory University (M.A. English.)