SBQ steelmaker Gerdau recently started up the new twin-tank vacuum degasser at its Monroe, MI, steelmaking operation. The same plant is the site of a four-strand continuous billet caster that started up in late 2012.
The new melt shop equipment is part of a $155.6-million capital-improvement program at that location, aiming to increase production capacity to 800,000 tons/year.
Gerdau’s North American special steel division produces special bar quality (SBQ) steel at electric mini-mills in Jackson and Monroe, MI, and Fort Smith, AR, for automotive and commercial vehicle programs, including forging billets. The group also processes steel products at five more locations.
Both the caster and the vacuum degasser were designed and built by Danieli SpA, the steel plant engineering group.
Vacuum degassing is a refining technology in which gaseous elements in molten steel are extracted under vacuum, which prevents oxidizing as required to produce various specialty and stainless grades. Danieli’s degassing technology includes a combination steam ejector/water ring or full-steam ejector pumps. The twin-tank configuration will allow Gerdau to produce specialty alloy grades in sufficient volumes to supply the billet caster.
Gerdau’s previous vacuum degasser will be converted to a ladle metallurgy furnace, according to Danieli.
The capital improvement program also will see Gerdau expand its rolling capacity by installing six more rolling mill stands and a new walking-beam reheat furnace by Q4 of this year. A new bar straightening and quality inspection station also will be in operation by the end of this year.
According to Gerdau, the rolling mill upgrades will allow it to increase the size of its billets to 210 mm square, which will increase the material reduction ratio and allow Gerdau to develop new products.
“This is a time of transformation for us,” stated Jack Finlayson, president of Gerdau’s North American special steel division. “We have experienced a few setbacks including weather and construction-related issues during this transition, but we have corrected them and are prepared to meet the growing demands of our customers.”
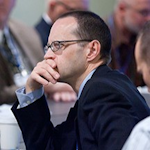
Robert Brooks | Editor/Content Director - Endeavor Business Media
Robert Brooks has been a business-to-business reporter, writer, editor, and columnist for more than 20 years, specializing in the primary metal and basic manufacturing industries. His work has covered a wide range of topics including process technology, resource development, material selection, product design, workforce development, and industrial market strategies, among others.
Currently, he specializes in subjects related to metal component and product design, development, and manufacturing—including castings, forgings, machined parts, and fabrications.
Brooks is a graduate of Kenyon College (B.A. English, Political Science) and Emory University (M.A. English.)