The costs of forged components are determined to a large degree by the material used to produce them. Correspondingly, material-cost savings have an enormous effect on the overall costs of the forged part. Furthermore, materials and heat treatment operations are closely tied together in the process chain. Ideally, optimizing materials will improve the potential for production cost saving, including energy costs in some cases.
According to Hirschvogel, this potential has now been realized with three different automotive applications — structural parts, case-hardened parts, induction-hardened parts.
The Hirschvogel Automotive Group manufactures forged steel and aluminum parts at eight locations worldwide, including four plants in Germany, as well as the U.S. (Columbus, OH), China, India, and Poland. It also holds a stake in a Brazilian joint-venture company, Mahle Hirschvogel Forjas S.A. Reportedly, the group’s 2013 output totaled 288,800 metric tons of forged parts.
For structural parts (e.g. common rail, wheel hubs, flanges), cost-efficient, precipitation-hardening ferritic-pearlitic steels are used, which achieve their strength properties through air cooling. If the mechanical properties of these steel products are not sufficient for the given application, heat-treatable steels are used, which demand quenching and tempering process, after which an inspection process is required to identify any hardening cracks.
The bainitic steel 16MnCr5mod (H2) — which was co-developed with steelmaker GMH —allows the mechanical properties of heat-treatable steels to be achieved with cost-effective cooling from the forging temperature. This results in considerable cost advantages compared to a part made of quenched and tempered steel.
For case-hardened parts, various case-hardening steels are available. The main differences among them concern the core strengths that may be attained. The core strength is decisive in determining the load-bearing capacity of the part. Greater hardenability has been gained to date mostly with expensive alloying elements. Here, too, 16MnCr5mod (H2) can lead to cost savings.
The alloying concept of H2 provides the steel with a level of hardenability (e.g. measured in Jominy values) that is comparable to the high-alloy case-hardening steels 18CrNiMo7-6 or 20NiCrMo6-5 — but with an alloy surcharge that is less than 20% of that imposed for high-alloy grades. This not only results in cost savings but also reduces significantly the volatility risk of fluctuating alloy surcharges.
A new material been developed for induction-heated parts, too. This steel, referred to as H50, achieves a grain structure with a strength value of between 900 and 1,100 MPa through controlled cooling from the forging heat and a surface hardness of over 60 HRC following induction heating. Depending on the application, parts with greater cost-efficiency or higher performance can be developed.
From these examples, it is clear that even in the area of forged materials there are new developments which lead to cost reductions or open up new technical possibilities. In the discussion between steel manufacturers, forging companies and customers, significant progress can be made here.
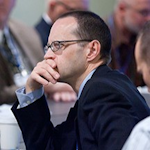
Robert Brooks | Editor/Content Director - Endeavor Business Media
Robert Brooks has been a business-to-business reporter, writer, editor, and columnist for more than 20 years, specializing in the primary metal and basic manufacturing industries. His work has covered a wide range of topics including process technology, resource development, material selection, product design, workforce development, and industrial market strategies, among others.
Currently, he specializes in subjects related to metal component and product design, development, and manufacturing—including castings, forgings, machined parts, and fabrications.
Brooks is a graduate of Kenyon College (B.A. English, Political Science) and Emory University (M.A. English.)