After a decade of poorly aimed, overly aggressive swings, I finally managed to break my grandfather’s axe—splintered it straight through in a spectacular explosion that left its aged head dangling by a thread. So it was time for an upgrade.
I went with a modern handle—fiberglass coated with squishy, shock-absorbing rubber (in an astonishing shade of yellow for no reason). Now it was only a matter of reattaching grandpa’s axe head to it.
And here I found myself in what may be familiar territory for MRO technicians out there. To affix the axe head, I knew I needed to use at least a two-part epoxy (resin plus hardener), and I knew that I had some tubs of each sitting around my workbench somewhere. What I didn’t know was the proper mix of each component (1:1? 1:2? 2:1?) or if whatever that proper mix is should be measured by weight or by volume or by some other complicated accounting. Directions were long lost along with the rest of the corroded labels.
It was a small job, though, so I didn’t worry too much. I just pried open the gunked-up tubs, dug out some bits that hadn’t hardened too much yet, and eyeballed a rough 1:1 mix. Applied it to the axe, let it cure for a day, and returned to my chopping.
It took one swing to break the epoxy’s grip on the handle. The second swing sent the head soaring out over the fence and into the woods.
The Problem
Besides the potentially catastrophic outcome of this axe repair experience, the overall scenario is a fairly common one on the plant floor, explains Chuck Eichacker, business and operations manager, engineering adhesives, at the St. Paul, MN-based epoxy maker H.B. Fuller.
“[Manufacturers] love to micromanage things down to cost per gram or cost per pound,” Eichacker says. “So there’s a temptation from the purchasing side to purchase drums—a drum of A and a drum of B—or even pail kits. And they think, ‘Look at that, we’ve saved 12% by bringing this product in by bulk!’”
While this approach may make strong financial sense, it presents some serious issues down the line for the worker who actually needs to use these epoxy mixtures. Because, as Eichacker aptly notes, “how that bulk is handled on the factory floor isn’t necessarily the first and foremost concern.”
This means, while plant personnel focus on core operations—producing the plant’s products at the rate they need—these giant tubs of epoxy get used up without much oversight. They are opened and closed every day by workers who demonstrate a wide range of care and protocols that, over time, cause the careful chemistries and processes that make these mixtures effective to fall apart.
There are a whole host of ways this can happen, Eichacker explains. “They may not measure it out in the proper ratio. Sometimes people can get confused and simply measure equal volumes rather than weights. Or, in the case of urethanes, they may not realize that if you don’t clear the headspace on the activator side, that activator will begin to absorb moisture from the atmosphere and start to go bad on you.”
As a result, he says, these giant, money-saving bulk orders can suddenly become giant liabilities. If used in assembly, this could mean parts pulling apart in shipping or in the hands of the customer, which leads to returns, complaints, and lost business.
Even more concerning, if used by maintenance, repair, and operations (MRO) personnel, this could mean failures in critical repairs that keep machines running and workers safe.
This, of course, is an extremely serious issue across the board, but it is also an extremely preventable one.
“I’ve had more calls than I care to remember where people say, ‘Hey, your adhesive is failing!’” Eichacker says. But after inspection “it becomes evident that the reason the adhesive is failing has nothing to do with the adhesive itself, but rather how it’s being handled.”
So what is the solution here?
For the production users, there’s the technology option, of course—upgrading to automated machines that can provide the perfect mixes right on the line where it’s used (and ensure proper care of the components between use, too). But for the MRO user, this kind of investment wouldn’t be nearly as effective.
“People that are responsible for maintaining factories are challenged and under pressure to make quick repairs,” Eichacker says. “So how can we support them by giving them solutions at their fingertips, in their toolboxes, that are convenient, fast, and reliable?”
The answer to that puzzle comes in the form of an entirely new line of products and delivery system that are custom-built for these users: GorillaPro.
The Adhesive Solution
Combining H.B. Fuller’s 100+ years of experience in creating adhesives with Gorilla’s well-known and highly respected brand resulted in a line of adhesives that was powerful enough to keep plants in operation and its people safe, but also mobile enough to be on-hand whenever it was needed, wherever it was needed.
The result of these efforts is a new product line for the MRO market. This line includes the EP3, EP5, and PU5, each of which offers their own set of unique characteristics and capabilities to meet the challenges these workers face.
First, the EP3 “Extra Fast Setting Epoxy” is a two-part structural adhesive that offers a work time of 3 to 5 minutes and settles to provide “several hundred psi bond strength within 15 to 30 minutes in the consistency of syrup,” Eichacker notes. After a full 24-hour cure, EP3 will provide between 1,500 and 2,500 psi lap shear value on clean and de-oxidized aluminum-on-aluminum applications. It is marketed as an ideal solution for repairs and bonding to a range of stone, metal, ceramic, plastic, and wood surfaces and can also be used on certain glass or carbon fiber applications.
The EP3 epoxy is the solution for ideal situations—nice, clean, horizontal surfaces that fit together in a perfect, uniform bond line. But in the MRO business, of course, things aren’t always quite so ideal.
“Epoxies love about 0.010-in. bond line, but that’s not always possible,” Eichacker explains. “So when we get a variable bond line or irregular surfaces, or something that’s on the vertical, we go with EP5.”
Like the EP3, the two-part EP5 epoxy offers a fast-setting and a strong hold on a wide variety of material substrates. But this product also includes a thixotropic filler that provides a thicker mix that is ideal for those less than ideal situations.
“What the thixotropic filler does for us is fill in regular gaps without running or dripping out,” Eichacker explains. “Also, if you put it on a vertical surface, it’s not going to immediately run or wick away, and if you squeeze something against it, it’s going to stay put.”
This additive also provides extra impact resistance and more flexibility when dealing with shear loads that would split apart pieces adhered with normal epoxies. This provides a mix that can act as a gap-filling adhesive for truly heavy-duty applications, from electrical to industrial fixtures where impact and vibrations are a concern.
And finally, we have PU5, the only polyurethane in the mix. Like the EP3 and EP5, the PU5 offers a fast setting, strong enough for mild handling and clamp release within an hour and a full set after 24 hours. What sets this one apart, though, is the flexibility it provides.
“Where urethanes do really well is on peel strength, whether it’s a 90-deg. peel pulling straight up or a 180-deg. peel, which is really challenging for a lot of adhesives,” Eichacker explains. This makes PU5 a powerful solution for flexible systems with a lot of movement in the bond area like belts or rubber stripping, damage to which some MRO technicians can encounter daily.
Taken together, what we have here is a full range of adhesives that seem enough to take on most conceivable issues that arise in the maintenance, repair, and operations environment across any plant or industry. This was, in fact, a central drive for the product launch.
“First of all, we had to understand the primary demands of the MRO market,” Eichacker recalls of the R&D process behind the GorillaPro line. “Then, how can we boil down what are thousands of different products available to us into something we like to call the ‘90% solutions’—three products that are going to solve 90% of the cases?”
After a year’s effort testing, discussing, and remixing designs, this process resulted in the EP3, EP5, and PU5 GorillaPro products.
However, finding the perfect adhesive mixes for this market only resolves half of the original problem.
The next challenge was to provide these mixes in a form factor and delivery system that allows MRO technicians to have ready supplies of them wherever and whenever they need them, and in a way that obviates the need for cans or pails of two-part adhesives for technicians to make precise measurements on the fly. In other words, H.B. Fuller had to help these harried workers respond faster with better solutions while also helping to prevent incidents like my axe “fix” from ever occurring.
This solution proved to be far simpler than finding the 90% solution, though equally ingenious as the adhesives themselves.
Finding the Right Mix
Rather than employing cans or pails of two-component adhesives, the entire delivery system for the EP3, EP5, and PU5 products is contained in a single, two-part foil pack containing both the resin and hardener.
“What we have now is essentially a 3.5-gram kit—about 1.75 grams of A and 1.75 grams of B—in these little packets,” Eichacker says. “So now you don’t have to store it in a hazmat locker in the corner of the factory. You throw these into your toolkit so if the technicians out there in the furthest 40 acres of the refinery or in the back corner of an assembly area need adhesives quickly, they can have an assortment of these three adhesive packets right there in the toolbox with them.”
With this, we have the full solution. Given H.B. Fuller’s goal to put “convenient, fast, and reliable” options at the MRO technician’s fingertips, these new mixes in this dispensing system—and packaged under the esteemed Gorilla logo—this seems to be awfully close to success. On paper at least.
Now it comes down to the field test.
Swinging for the Fences
To do this, I went back to my original failure, affixing a very old axe head on a very new axe handle—a job that requires strong impact resistance between two parts that refuse to align uniformly. Seems like a perfect test for the EP5.
After an afternoon of prep work (removing all traces of the failed adhesive and filing away a few decades worth of corrosion), I set to work. This time, there was no prying open dried-up tubs, no guestimating volumes, no room for user-error. I simply folded the pack in half, snipped it open, and emptied the contents onto some spare cardboard. A quick stir and I was ready to apply.
My first impression was that this thixotropic filler absolutely lived up to Eichacker’s hype—I was able to apply it to the full 360-deg. contours of the junction point without experiencing any drip or run. As a particularly sloppy, error-prone handyman, this was well-appreciated.
Likewise, the gap-filling characteristics provided what felt like a secure, snug fit between these two oddly paired components—a fit that felt settled and strong after just 4 minutes.
The next evening was the real test. I have this troublesome hardwood stump I’ve been hacking at for months with little progress (besides busting my axe), so it became my target.
The EP5 survived the first swing. It survived the second. An hour later, after a steady volley of too hard, too wild swings, this single packet-worth of epoxy was still holding strong—much stronger at that point than my exhausted back.
I called it there. This stuff clearly works.
Based on this experience, it seems as though H.B. Fuller has filled a real hole in the MRO toolbox—a handy assortment of adhesives, sealants, and lubricants designed for repair, installation, and maintenance challenges.
But we’re not just leaving it there. As part of H.B. Fuller’s launch of the GorillaPro line, it is out to get these adhesives into the hands of as many MRO specialists as possible. So the company agreed to provide 10 lucky NED readers with a sample pack to test out in the real world.
You can take your shot at winning your sample by registering here: NewEquipment.com/21146337.
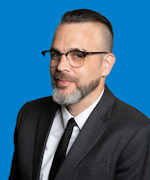
Travis Hessman | VP of Content, Endeavor Business Media
Travis Hessman is the VP of Content for Endeavor Business Media. Previously, Travis was the Editor-in-Chief for Industry Week and New Equipment Digest as well as the Group Editorial Director for Endeavor's Manufacturing Group.
He began his career as an intern at IndustryWeek in 2001 and later served as IW's technology and innovation editor. Today, he combines his experience as an educator, a writer, and a journalist to help address some of the most significant challenges in the manufacturing industry, with a particular focus on leadership, training, and the technologies of smart manufacturing.