Machine builder SMS has been contracted by Turkey’s Parsan Steel Forging and Machining Co. (Parsan Makina Parçaları Sanayii A.Ş.) to design and build a new 25-MN closed-die press, one capable of forging up to 5 million pieces annually, mainly pistons and flanged hubs. Parsan forges carbon, quenched and tempered (QT), micro-alloyed, and stainless steel, as well as customer-specific grades, for automotive, truck, off-road machinery, and heavy equipment markets.
The contractor did not indicate the value of the contract award, nor the installation schedule for the new press.
The closed-die press will be installed at new forging and machining complex under development at Dilovası, east of Istanbul, which Parsan describes as one of the largest operations for engine, drivetrain, and large forgings serving the European market.
SMS detailed that the AMP 2500 press will be the center of a highly automated process, including an electrically driven walking-beam delivery for feedstock, mechanically coupled and retractable die spraying, programmable ejectors, and a quick die-change system.
It explained that its EHA automatic electric walking-beam systems is comprised of four individual housings with the drive situated outside of the press frame, preventing contamination from scale and dirt. The system ensures “a finely balanced and smooth motion” due to a separate drive consisting of servo motors, with dedicated gears for each axis.
The three axes of motion are transport step, lifting/lowering and opening/closing. Travel, speed, acceleration and deceleration of the individual servo axes are automatically synchronized, SMS noted. The EHA system maintains short cycle times while minimizing shock loads on the mechanical elements by optimizing acceleration and deceleration curves during each movement.
Simultaneously, the material transfer sequence of the EHA is maximized for efficiency by constant monitoring of the position of the press ram. The automatic walking-beam system triggers the press stroke, according to SMS.
The contractor also detailed the its pivotable spray manipulator, located on the back of the press. This SE system is arranged so that the die holder with dies is freely accessible from the front. The spray manipulator is controlled together with the ram movements by mechanical coupling, thus ensuring the position of the system corresponds precisely at all times to the position of the ram and walking beam. Spraying times for individual processes are individually programmable. For retrofitting and maintenance work, the manipulator can be swiveled out of the press area.
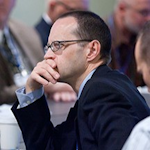
Robert Brooks | Editor/Content Director - Endeavor Business Media
Robert Brooks has been a business-to-business reporter, writer, editor, and columnist for more than 20 years, specializing in the primary metal and basic manufacturing industries. His work has covered a wide range of topics including process technology, resource development, material selection, product design, workforce development, and industrial market strategies, among others.
Currently, he specializes in subjects related to metal component and product design, development, and manufacturing—including castings, forgings, machined parts, and fabrications.
Brooks is a graduate of Kenyon College (B.A. English, Political Science) and Emory University (M.A. English.)