Everyone knows artificial intelligence has the potential to transform manufacturing: optimizing performance by taking all that data in the plant and supply chain and making it work better, faster, and automatically. And experts believe these changes are coming soon. By 2030, PwC predicts AI will add $6.6 trillion in productivity alone to the global economy.
What isn’t touted as loudly, though anyone who has tried adding it to their operation will probably tell you, is that AI ain’t a magic wand. It might not even be a tool sharp enough to cut through your particular problems. An IDC survey found a quarter of organizations reported up to a 50% failure rate.
That makes it tough on IIoT companies such as Flutura Decision Sciences & Analytics, a startup that launched its platform Cerebra in 2013. In fact, they don’t even like to say AI.
“There’s still a little bit of misconception and ultimately what [artificial intelligence] can deliver and what vendors are actually selling,” Flutura general manager Greg Slater says. “Quite honestly we don’t like to use the term ‘AI’ often because of all the misconceptions in the industry. We like to call it ‘reliable industrial intelligence.’”
On the surface, the Cerebra SignalStudio platform, which improves machine operations for oil & gas, specialty chemical and heavy machinery industries, works just like any predictive-preventative maintenance solution would. It employs sensor and machine data and cloud-based AI to diagnose and prevent failure and downtime, while maximizing asset performance reliability and uptime and increasing yields and quality outcomes.
Where it differs is in its use of NanoApps, premade solutions tailored to specific industries and issues. These include the Drilling Efficiency App, Pressure Pumping App, Quality Bench Marking App, Quality Simulation and Prognostics App, and Yield Optimization App. It can detect welding defects using image analytics or flag dangerous work environments with video analytics, such as a slippery floor or person not wearing PPE.
“We’re not an AI platform that is trying to boil the ocean; we have a very surgical approach,” Slater explains.
The Houston-based company fancies itself the “FitBit for Machines,” which is appropriate as the company founded in 2012 was conceptualized to help the medical industry before it settled on the IIoT.
Flutura has about 30 clients currently, with adhesive manufacturer Henkel being the standout. Flutura helped predict a quality issue that resulted in solving “a $300 million problem,” Slater says.
The adhesives Henkel makes must meet very stringent specifications, as Bombardier uses them to bond its airplane wings. At Henkel’s Shanghai Dragon plant, Cerebra started by looking at historical data along the entire production line to get a baseline for quality and what affects it. Then it started to predict what materials must change based on environmental factors and ultimately act to prevent bad batches, which could lead to wasted time and product.
Each successful deployment adds to the efficacy of these NanoApps.
Slater says the Quality Simulation and Prognostic apps got implemented at Henkel’s Dragon plant has scaled up to more than 120 manufacturing lines across 15 countries for just two customers.
The agile startup, which has been named to Gartner’s Magic Quadrant for IIoT for the past two years, makes a bold promise to customers that despite industry statistics, this solution won’t fail them.
“We guarantee that our customers, through our different AI applications, will see value within 90 days or less,” Slater says. “In the current environment, most of these initiatives are designed as multi-year projects with benefits delivered almost at the end of the cycle.”
In one case, Flutura set up a digital twin for a crude oil extraction machine in 48 hours. An array of 500 sensor tags continuously stream machine data to Cerebra to ensure the high pressure (up to 9,000 psi) is not building up to a failure—and in oil & gas, one hour of downtime could cost $200,000. Slater believes that through a combination of digital twins, real-time visibility and remote monitoring, there’s an opportunity to unlock $8 billion worth of savings in the producing field.
Cerebra also manages by exception, or finding the data or machine that doesn’t match the digital twin.
“We ignore the healthy assets and look at unhealthy processes,” Slater says. “Then we drill down to root cause analysis and take action against that and get that info out to the field.”
This helps prioritize human assets that may have to drive to 50 oil wells in a day or travel across miles of factory floor space. The technician or engineer goes to where the anomalies are first, instead of a scheduled route, which can help detect small problems before they turn into expensive ones.
And while the AI will get all the credit, the human element is not forgotten. Along with first-principles based models and equations and real-time data, Cerebra adopts the tricks of the trade coded within experienced workers’ brains, codifying the tribal knowledge for the entire organization to use.
“Real value is realized when all three sources of data are leveraged together,” Slater says.
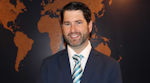
John Hitch | Editor, Fleet Maintenance
John Hitch, based out of Cleveland, Ohio, is the editor of Fleet Maintenance, a B2B magazine that addresses the service needs for all commercial vehicle makes and models (Classes 1-8), ranging from shop management strategies to the latest tools to enhance uptime.
He previously wrote about equipment and fleet operations and management for FleetOwner, and prior to that, manufacturing and advanced technology for IndustryWeek and New Equipment Digest. He is an award-winning journalist and former sonar technician aboard a nuclear-powered submarine where he served honorably aboard the fast-attack submarine USS Oklahoma City (SSN-723).