Allegheny Technologies Incorporated is planning an estimated $70-million expansion of its nickel-based superalloy powder production capacity, responding to demand for specialty materials for jet engine parts. Those parts are mainly forgings and milled products, but ATI also noted rising demand for additive manufacturing materials, including parts used in aerospace, medical, electrical energy, and oil-and-gas markets.
ATI forges carbon and alloy steels as well as superalloys, using isothermal and hot-die forging processes.
According to ATI chairman Rich Harshman, the superalloy expansion project will strengthen the group’s position in a technically demanding field that is critical to supplying aerospace engine manufacturers.
Superalloys are alloyed materials that exhibit multiple critical characteristics, such as mechanical strength, creep resistance, corrosion or oxidation resistance, for example. They are used to form parts for the high-temperature regions of gas turbines, including turbine blades and disks. Nickel-based superalloys are selected because of their performance in the high heat and stress of those operations.
The alloys are refined into powder forms that are later converted into ingots by electroslag melting and vacuum refining. Powder metals also can be sintered (e.g., by direct metal laser sintering, an additive manufacturing method) into parts via 3D printing.
ATI said the two-year expansion at its Monroe, NC, ATI Specialty Materials business would be self-funded, and is included in its current $200-million multi-year capital improvement program.
ATI’s existing powder refining operation at Oakdale, PA, is operating near capacity, the company said.
“A significant portion of the powders to be produced from this expansion are needed to meet requirements of existing long-term agreements with jet engine OEMs that run well into the next decade,” according to Harshman, who also holds the titles of president and CEO. “The expansion also better positions ATI to continue as a leading innovator supplying advanced powders to the new and rapidly growing additive manufacturing industry.”
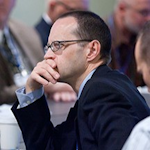
Robert Brooks | Editor/Content Director - Endeavor Business Media
Robert Brooks has been a business-to-business reporter, writer, editor, and columnist for more than 20 years, specializing in the primary metal and basic manufacturing industries. His work has covered a wide range of topics including process technology, resource development, material selection, product design, workforce development, and industrial market strategies, among others.
Currently, he specializes in subjects related to metal component and product design, development, and manufacturing—including castings, forgings, machined parts, and fabrications.
Brooks is a graduate of Kenyon College (B.A. English, Political Science) and Emory University (M.A. English.)