Alcoa has started construction of the $90-million operation to produce aluminum-lithium alloys in a new, 115,000-ft2 operation at its complex in Lafayette, IN. The new operation will cast over 20,000 metric tons/year of Al-Li metal in round or rectangular ingots. The ingots will be available for rolling, extruding, or forging.
Production will start by the end of 2014, Alcoa stated. The investment is being supported by the Indiana Economic Development Corp., a state agency.
“Our aluminum lithium supply chain will be the premier operation in the world and this specialty alloy will be flying on the next generation of aircraft," explained Eric Roegner, president, Alcoa Forgings and Extrusions.
Aluminum-lithium alloys are significantly less dense than standard aluminum alloys, containing up to 2.45 wt% of lithium. Lithium is the lightest of all solid metals (though highly reactive, and thus requiring particular skill in handling and manufacturing.) Because of these factors, and the costs associated with them, the principal applications for Al-Li alloys have been in aerospace and defense applications.
Last year Alcoa introduced a series of Al-Li alloys as an alternative to composite materials, and said these patented materials would allow aircraft OEMs to build lighter, lower-cost airframes. It uses these alloys in forgings, extrusions, and sheet and plate products for aircraft structures, including wing and fuselage structural elements.
"Our primary role as aerospace solution providers is to help the OEMs reduce fuel consumption per seat mile," according to Roegner. "We have a long history working with aerospace customers to help new aircraft meet demanding new missions and provide optimum solutions for both the engine and airframe structure.
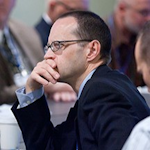
Robert Brooks | Editor/Content Director - Endeavor Business Media
Robert Brooks has been a business-to-business reporter, writer, editor, and columnist for more than 20 years, specializing in the primary metal and basic manufacturing industries. His work has covered a wide range of topics including process technology, resource development, material selection, product design, workforce development, and industrial market strategies, among others.
Currently, he specializes in subjects related to metal component and product design, development, and manufacturing—including castings, forgings, machined parts, and fabrications.
Brooks is a graduate of Kenyon College (B.A. English, Political Science) and Emory University (M.A. English.)