A machine described as “the world’s most powerful clutchoperated screw press” was commissioned during the summer at China’s Wuxi Turbine Blade Co. Ltd., in Jiangsu. SMS Meer designed and built the installation, which has an impact force of 35,500 mt, and completed the project three months ahead of schedule. It said the new press would allow WTB to produce forgings of high-strength alloys, for power plants and the aircraft manufacturing.
“For us the plant has the advantage of being able to meet the growing demands of our customers from the aircraft and power plant industries,” according to Wuxi Turbine Blade managing director Yan Qi,
The forger has been working with SMS Meer (www.smsmeer. com/en) since 1976, and ordered its first large press in 1995. SMS indicated the experience of their long cooperation contributed to the successful installation and commissioning in just nine months, and well ahead of the contracted date.
During the installation period, SMS updated the components of the previously installed press, and it trained the machine operators. The staff had already been trained to operate and maintain the machine’s hydraulics, controls, and electronic systems.
According to the builder, the new plant combines the benefits of a forging hammer with a hydraulic press, so fewer strokes are required to complete a forging. “This means that the machine guarantees high forming forces with short workpiece contact time,” SMS stated. “At the same time, the material microstructure remains homogeneous. WTB thus profits from high productivity and quality.”
SMS Meer engineered the project from its engineering center in Mönchengladbach, Germany. The machine stands 23-ft high, and at its heart is the 1,320-mm diameter screw weighing 85 mt. The press is powered by a 500-kW variable-frequency drive, however, which SMS indicated is 87% less power than would be required by a conventional screw press of similar scale, but with a simultaneous increase in forming energy.
Beyond energy efficiency, the press is designed with variable impact-speed dies, so WTB is ready to forge parts that are more sophisticated, as required by manufacturers in its aerospace and power-generation target markets.
The machine’s crossbeam is a casting that weighs 325 mt, and its press table weighs over 300 mt. In addition to the design and commissioning, the Wuxi Turbine Blade project involved some logistical success: SMS delivered both castings and installed each one within one-tenth of a millimeter, as identified by the design plan.
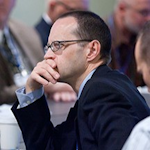
Robert Brooks | Editor/Content Director - Endeavor Business Media
Robert Brooks has been a business-to-business reporter, writer, editor, and columnist for more than 20 years, specializing in the primary metal and basic manufacturing industries. His work has covered a wide range of topics including process technology, resource development, material selection, product design, workforce development, and industrial market strategies, among others.
Currently, he specializes in subjects related to metal component and product design, development, and manufacturing—including castings, forgings, machined parts, and fabrications.
Brooks is a graduate of Kenyon College (B.A. English, Political Science) and Emory University (M.A. English.)