Streamlining Material Requirement Planning for Raytheon
As one of the world’s largest aerospace and defense (A&D) firms, Raytheon is responsible for delivering a substantial volume of highly complex products and services within stringent cost, schedule, and quality constraints. As such, Raytheon relies on a global, multi-tier network of suppliers — including forgers — and it must ensure that each supplier provides the required quantities of goods at precisely the right time to keep its customer orders on track, while minimizing inventory-related cost and handling. Developing and communication these timelines is done via the material requirement planning (MRP) process.
Over time, each of Raytheon’s six business units developed its own MRP processes, and these were executed by one or more MRP systems: the organization had a total of nine MRP systems running at once, each of which generated new schedules weekly.
Regardless of the MRP solutions in place, each business unit faced a common challenge. In order to protect the integrity of the MRP systems and the information they contained, Raytheon mandated that none of its MRPs could be integrated directly with any suppliers’ systems. This meant all coordination between Raytheon and its suppliers had to be conducted manually, including: purchase order acknowledgement, MRP modifications, and “place and chase” -- the impractical task of tracking and prompting suppliers to reconfirm orders and deliveries.
With over 1 million purchase orders each year, and an average of 2-3 changes per PO, Raytheon recognized that high level of human intervention in its MRP process did more than consume resources: it created unnecessary risks, including miscommunications between buyers and suppliers; lost documentation; and unintentional errors as buyers and suppliers updated MRPs manually.
Raytheon understood the importance of encouraging collaboration throughout the MRP process between its own buyers and their suppliers, but did not want to overhaul the existing infrastructure in order to do so. There would be considerable time, cost, effort, and confusion to a major MRP process overhaul.
Exostar’s Supply Chain Platform (SCP) circumvented those concerns. SCP is a multi-enterprise supply chain collaboration program for the A&D industry, offered via a Software-as-a-Service model. Raytheon received a proven, ready-to-execute capability that limited its upfront cost and encouraged phased implementation.
Initiating Tighter Integration
Raytheon initiated a tight integration with SCP, thanks to Exostar’s security standards. SCP’s flexible, service-oriented architecture and extensive library of supported standards and protocols meant the solution could be integrated seamlessly and expeditiously into the operating environments of Raytheon and its suppliers.
Raytheon had previously deployed a communications bus and integration gateway called cHub, which brought further advantages: SCP connects directly with cHub and the MRP systems at any of Raytheon’s business units could be left predominantly intact. Buyers could continue using the MRP system interfaces, documents, and procedures with which they were accustomed, yet transactions including POs and PO Changes could flow electronically to SCP through cHub.
Raytheon’s Integrated Defense Systems (IDS) group was the first business unit to transition to SCP and migrate its legacy MRP process to a collaborative MRP (cMRP) process, connecting its existing MRP systems with SCP.
Exostar worked with Raytheon to train buyers and selected suppliers, and to “on-board” them to SCP. SCP controls the transactions associated with planning, scheduling, and delivery of goods for IDS buyers and their suppliers. Specifically, SCP enables automated processes, simplifying constituents participation in weekly cMRP scheduling updates.
All relevant documents are exchanged and archived in SCP throughout the cMRP process. It also offers reliable alerts/notifications of schedule dates and requirements, and allows buyers and suppliers to exchange shipping notices and receipts without fear of lost records or data.
By minimizing the need for data re-entry, printing and faxing of documents, as well as phone- and email-based communication and coordination throughout the cMRP process, SCP delivered the advantages IDS anticipated: a reduction in administrative and overhead expenditures; virtual elimination of manually induced errors; and an opportunity for buyers and suppliers to work together even more efficiently.
SCP’s Information Manager component extends the benefits by providing comprehensive visibility into interactions and performance throughout the cMRP process – in real-time and over the course of time. Executive dashboards and reports promote greater collaboration and accountability across the supply chain, enabling buyers to create supplier scorecards. Because Information Manager allows anomalous conditions to be identified quickly, IDS can manage by exception, no longer requiring personnel to scrutinize each transaction in detail. Consequently, the cMRP process executes more consistently and smoothly, leading to improved supplier performance with regard to fulfilling commitments on-time and on-budget.
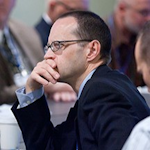
Robert Brooks | Editor/Content Director - Endeavor Business Media
Robert Brooks has been a business-to-business reporter, writer, editor, and columnist for more than 20 years, specializing in the primary metal and basic manufacturing industries. His work has covered a wide range of topics including process technology, resource development, material selection, product design, workforce development, and industrial market strategies, among others.
Currently, he specializes in subjects related to metal component and product design, development, and manufacturing—including castings, forgings, machined parts, and fabrications.
Brooks is a graduate of Kenyon College (B.A. English, Political Science) and Emory University (M.A. English.)