Among successful manufacturers there is little doubt about the factors that keep their enterprises thriving and growing: product excellence, production efficiency, and customer satisfaction. Those qualities are for the world outside the operation to recognize and appreciate. Within successful organization, at the point where strategies are set, programs are planned, and actions are carried out, there is an additional factor: All successful manufacturers have programs for establishing, maintaining, and improving workplace safety.
The rewards for outstanding workplace safety are not obvious, except to the workers, managers, and investors in those manufacturers. Among forging operations, the best workplace-safety performances are recognized annually by the Forging Industry Association, which identifies its members’ accomplishments with Its FIA Safety Awards, based on statistically verifiable achievements.
Recently, 17 FIA member companies were recognized with awards for the 2015 accounting period.
Tracking and documenting workplace safety must be managed carefully and thoroughly, and the FIA takes an appropriately though approach to evaluating members’ performance. Each year the Association surveys member companies to document safety records at individual plants, tracking OSHA reportable Incidence Rates and Frequency Rates at different plant sites to identify the leading plant-safety performers in the industry. The annual awards are presented to forging companies in four groups, according to the average annual employment at each location.
FIA collects data on plant safety records via questionnaires delivered annually to all its producer members. Each plant provides data recorded on OSHA Form No. 300, “Summary of Occupational Injuries/ Illnesses for Calendar Year” for U.S. companies, and from Worker’s Compensation Reports for Canadian companies on the questionnaires.
FIA presents first-, second-, and third-place Safety Award plaques to plants that have the lowest Recordable Cases Incidence Rate, provided that the DART Incidence Rate falls below the group average. In the event that Recordable Incidence Rates are equal, FIA assigns the award to the plant with the lower DART Incidence Rate.
Awards for improvement are presented too, to plants that demonstrated the greatest decrease in the DART Incidence Rate. This is determined by percentage of improvement by DART Incidence Rate compared with the average of the preceding three years.
A certificate of recognition is awarded to each company that does not earn a first-, second-, or third-place rank, and where the Recordable Incidence Rate falls below the group average — provided that the DART Incidence Rate also falls below the group average.
Success is Certifiable — Each year FORGING seeks details of the successful forging industry workplace-safety programs by interviewing, confidentially, the principle figures managing the award-winning programs. Their insights make it plain that winning FIA’s recognition, indeed achieving the documentable standards that establish successful workplace safety results from “creating and maintaining a company culture focused on safety and quality,” as one of our correspondents explained.
Achieving such a culture is a general objective. Accomplishing that objective involves building strategies, defining procedures, and executing tasks with an increasing degree of specificity. “As part of our daily operations and our quality system, all our employees are trained in a continuous manner,” he detailed further. “Training ranges from correct use of safety gear, process and products, industry best practices and prevention methods. The foundation of our system is based on strong values and a solid production methodology striving for flawless execution.”
Another award-winning correspondent added that having certified accountability for lost-time and DART rates ensures the success of his plant’s safety program. “In our operations, middle and upper management are responsible for the safety of the personnel,” he emphasized. “If the management has an active role in safety, obtaining the safety targets is possible.”
Furthermore, we learn from these successful operations that each plant must thoroughly and regularly assess its specific, current safety conditions and devise its program in response to those. “We have focused our efforts in reducing natural rotation of our employees,” we learned from one correspondent, “creating a solid task force and maintaining the knowledge generated through the years, in this way we guaranty a continuous improvement in all fronts of our operation.”
He continued, for emphasis: “We have formed a team of trained experts which, shift by shift, audit our process and the complete facility, always looking for areas of improvements focused on safety and health.”
We learned, also, that successful safety strategies maintain a constant focus on target objectives: “We conduct five-minute pre-work meetings at the start of the day each day,” according to one correspondent. “The theme is based on the needs of the production area, or it may be of an incident that has occurred in another facility.”
In addition, this particular forging operation has established dedicated functions to provide the resources that managers must have to keep the safety focus effective and operative. “We have a Training Facilitator department (CDC) that follows-up on all worker training,” he relayed. “Each training module includes a section safety principles and practices.”
Track Facts, Set Goals
Accounting for safety is a non-negotiable detail of any workplace-safety improvement program. Most effective programs will take care to track leading indicators of workplace accidents and injuries (e.g., near misses, employee engagement in safety efforts, good housekeeping) as well as the actual details (i.e., trailing indicators, meaning specific injury incidents and illness rates.)
“- Besides close tracking of Injury and Illness rates we follow-up on days away from work that result in severity rates,” noted one correspondent, who added that monitoring attendance at “safety” meetings underscores the importance of program to workers and promotes proper adherence to safety practices throughout the workplace.
“We have designed and maintained a strong tracking system focused in improving on safety and health related events,” we learned from one FIA Safety Award winning location. “No event can go unsolved, not understood, or without an improved solution. We apply the lessons learned in one event to the entire facility via weekly training class of different types.”
Winning awards is a worthy objective, but establishing (or reestablishing) workplace practices that inculcate safety compliance and ensure measurable results is the reliable course to improving safe operations.
“Create a system that enables your facility to be engaged in all aspects of your operation,” our correspondent advised. “Safety is always first and it is nonnegotiable; you operation should not tolerate any expression against safety in you company. Initially it will be difficult; in time, your team will thank you.”
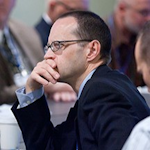
Robert Brooks | Editor/Content Director - Endeavor Business Media
Robert Brooks has been a business-to-business reporter, writer, editor, and columnist for more than 20 years, specializing in the primary metal and basic manufacturing industries. His work has covered a wide range of topics including process technology, resource development, material selection, product design, workforce development, and industrial market strategies, among others.
Currently, he specializes in subjects related to metal component and product design, development, and manufacturing—including castings, forgings, machined parts, and fabrications.
Brooks is a graduate of Kenyon College (B.A. English, Political Science) and Emory University (M.A. English.)