Robotics Trends Shaping Performance
The role of automation in forging operations, and particularly the role for robotics, is not a new development, as it is in some manufacturing operations. The power necessary to handle large and heavy (and hot) forging workpieces; the repeatability needed for the task; and the risk to human workers, made robots welcome in the forging operations of all styles and sizes.
What is new are the various technological and functional trends in robotic automation, and how those offer opportunities for forging operators to achieve the key performance indicators that define advanced manufacturing operations.
For example, consider “flexibility” and “reliability.” ABB Robotics recently introduced a smaller version of its severe-duty automation device, the IRB Foundry Plus 2. The device is kitted to withstand the heat, dust, and other environmental hazards for robots in demanding, repetitive processes, like tending a forging press. It carries the requisite IP66/67 protection ratings, from base to wrist, meaning that the robot’s electrical compartments are sealed against liquid and solid contaminants. The device is also resistant to corrosion, and will withstand high-pressure steam washing.
The IRB 1200 Foundry Plus 2 is an update to the IRB 1200 introduced just two years ago, and according to the developer it is the smallest foundry-duty robot in its class. As for its applications, ABB Robotics foresees increased flexibility and reduced cycle times for precision processes, for example, placing, positioning, and transferring workpieces in high-volume forming and finishing.
The IRB 1200 is available in two variants that can handle a wide range of applications and are cost effective due to commonality of parts. The 700-mm reach variant can carry a payload of up to 7 kg, while the longer-reach, 900-mm variant can carry up to 5 kg of payload. “This robot will allow our customers to increase productivity, deliver better work piece quality, and reduce cycle times,” according to Dr. Hui Zhang, head of product management for ABB Robotics.
Now, consider “energy efficiency”: forging operations are huge volume consumers of energy, and handling functions are a steady contributor to that total. Dango + Dienenthal Maschinenbau (DDS) develops robots and transport manipulators for forging and ring rolling, and recently adopted electromechanical servo-drive technology to power its heavy-duty robots to the market. These robots, with load capacities ranging from 500 to 15,000 kg, exceed the performance of standard robots for forging because they can perform at a range up to 10.5 m from the machine axis to the gripper plane of the tongs. These devices’ high load torque is achieved by a special lever system and hydraulic drives, which can incorporate advanced control technology and integrated position sensors, thereby achieving high-accuracy part positioning.
In manual control mode, these robots can be controlled by the press operator or from a control room, to handling small to medium-sized lots flexibly. For large batches, once the program is set-up production processes can be fully automated, taking into account individually programmed safety protocols and the specific requirements of the equipment and work space.
In recent years DDS has replaced the robot devices’ central, hydraulic drives with decentralized electromechanical drives, in suitable load areas. Electromechanical cylinders, with high-load spindles and driven by servomotors, have the ability to deliver high force at high speeds, with controllability and high energy efficiency.
Adopting electromechanical servo-drive technology for heavy-duty robots conserves the energy required to power a continuously running hydraulic pump, and it eliminates the necessary energy form transformations from the electric pump drive to the hydraulic cylinder movement; both of these factors make a DDS electromechanical robot more energy-efficient than a hydraulically driven unit.
In operation, an energy-recovery system feeds the braking energy of the respective axle drives back to the circuit of the converters, so the overall energy consumption is reduced further. By combining servo inverters and motors with integrated encoders, acceleration and speed in the control can be determined. This makes it possible to move all machine axes at their respective maximum speeds, and at the same time to protect the machine structure from excess stress and undermining the machines’ accuracy in timing and placement. This represents another competitive advantage over hydraulically powered forging robots
Also, the robot arm’s lever system is updated with DDS electromechanical servo-drive technology. As a result the lever system is compact and "weight-optimized," with increased stiffness. The mechanical movement of the gripper in the horizontal direction relieves the feed drive from the weight force of the workpiece. By eliminating various hydraulic components (e.g., pumps, tanks, valves and piping), heavy-duty robot is minimized overall. By adopting a new energy source, the robots necessary for typically large and demanding forging processes become more accurate and energy-efficient.
Perhaps the most intangible KPI for manufacturers is “responsiveness,” the ability to make advanced technology perform as necessary, to execute production processes as required to meet customers’ requirements or enterprise performance goals. Programming robots properly demands operators with increasing skill levels, but also control technology that is accessible as well as powerful.
ABB Robotics offers RobotWare 6, an updated controller software with an extensive toolbox for developers and a broad range of communications capabilities. The updates reportedly improve programming and control of robotic systems and equipment, and continues to offer a high level of motion control and process safety.
RobotWare 6 improves the programmers’ installation process, with the “Installation Manager” function highlighted by a flexible application licensing mechanism for developers, and a new, intuitive user interface that improves robot set-up time and system reconfiguration.
Another feature of RobotWare is “Externally Guided Motion” (EGM), which, with the aid of external sensors, provides operators with more precise control over robot motion. This function allows system integrators to optimize work cell design and production flow, and the sensors provide the ability to input absolute positions, and to modify the robot’s path. Paths can be updated every four milliseconds with a controller lag of between eight to 20 milliseconds, depending on the type of robot.
Further, RobotWare 6 shortens program installation time, makes jogging more responsive, and accelerates restarts, all combining to provide improved productivity.
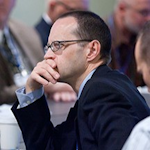
Robert Brooks | Editor/Content Director - Endeavor Business Media
Robert Brooks has been a business-to-business reporter, writer, editor, and columnist for more than 20 years, specializing in the primary metal and basic manufacturing industries. His work has covered a wide range of topics including process technology, resource development, material selection, product design, workforce development, and industrial market strategies, among others.
Currently, he specializes in subjects related to metal component and product design, development, and manufacturing—including castings, forgings, machined parts, and fabrications.
Brooks is a graduate of Kenyon College (B.A. English, Political Science) and Emory University (M.A. English.)