More complex geometries and near-net-shape production are making necessary for cold-forging lubricants to withstand higher mechanical and thermal stresses, to reduce friction, and prolong tool life. The tribological conditions in cold forging are extremely severe. Interface tool temperatures up to several hundred degrees combine with surface expansion factors up to 3,000%. Thus, the lubricants are subjected to extreme conditions, and failure to withstand those conditions will promote defects on the workpiece and galling or damage to the die.
Cold-forged components are highly valued for automotive design: By offering nearly complete material usage, superior material properties, and tight geometrical tolerances, cold-forged parts save cost and deliver excellent results. The successful application of cold forgings is closely related to an efficient lubrication system.
The most common lubrication system, known for its effectiveness at withstanding all the above-mentioned conditions, is the zinc-phosphate coating with some additional soap-based lubricant. Although the performance of this solution has been proven over time, recently it has been rejected as an environmentally unfriendly tribosystem, as regards both the workplace and the global environment. The globalization of industrial production has forced the forging industry to look for a better solution.
Addressing Conventional Zinc-Phosphate Lubrication
The conventional zinc-phosphate coating-based lubricant is a two-part conversion system, consisting of a pre-coat (in this case, the zinc) used as a lubricant carrier, and the lubricant itself. Bonding to the billet, the pre-coat forms a protective surface on the metal and prepares the billet for subsequent coating with the lubricant.
After the billet has been coated with the zinc phosphate, it is submerged in a soap-based lubricant bath or in extrusion oil. This procedure activates a chemical reaction that enhances the adhesion of the lubricant to the billet, which results in increased corrosion protection, improved friction properties, and better resistance of the lubrication film against surface enlargement during forging.
The process of zinc-phosphate coating can be summarized as three main steps: cleaning (surface preparation), chemical bonding of the conversion coating of zinc phosphate to the metal substrate, and lubrication.
- Mechanical cleaning processes such as shot blasting and peeling prepare the surface of the billet for better adhesion of the zinc phosphate. After all these operations the surface is rinsed with water to neutralize the remaining acid and to eliminate any risk of further contamination.
- After it has been properly cleaned, the billet surface is next subjected to phosphating, and zinc phosphate is chemically bonded to the metal base. Prior to lubrication, the workpiece is thoroughly rinsed again.
- After rinsing, the billet is coated with a lubricant while dipped into a hot bath of alkaline soap (typically sodium stearate) that reacts with the zinc phosphate and forms zinc stearate. The process ends with the drying of the billet.
Although well known for its undoubted advantages of strong adhesion and improved corrosion protection, the zinc-phosphate coating possesses far too many disadvantages.
The biggest disadvantage of conventional lubrication systems is that they contain different chemicals that lead to hazardous waste handling and disposal. During the process, the baths become polluted with heavy metals like lead and cadmium. Sludge, containing dangerous pollutants in both the bath and wastewater, is generated. The majority of the baths and used water cannot be recycled and must be treated as hazardous waste. In addition to these reasons, phosphating process requires large amounts of water, energy, and longer treatment time than new tribological systems.
There is no doubt that the pre-lubricant coating is critical for the quality of every cold-forged piece. However, the conventional way raises too many environmental concerns and therefore leading companies have already started to work on alternative processes.
Among the most promising alternatives to the zinc-phosphate lubrication system are polymer-based coatings. The attempts for better lubrication systems have developed in two directions: new conversion coatings and lubricants without conversion coating.
Using different tests—such as the sliding compression test, the double cup extrusion test, and the ring compression test—helps to determine the high friction coefficient of a new lubrication system. It is very difficult to find a high-quality lubrication solution for multi-stage forging operations, where adhesion is essential and tools get worn easily. Both, the lubricant itself and the surface treatment are of critical importance. The lubricant’s chemical composition has a significant impact on the tribological conditions. Moreover, surface finishing is crucial because reduced surface roughness decreases friction significantly.
New Conversion Coating Options
The new conversion coatings act in a similar way as the conventional zinc-phosphate-based lubrication system but eliminate most of its drawbacks by applying improved techniques.
Electrolytic Phosphate Conversion Coating
The main advantage of this process is the sludge-free phosphating bath. The applied lubricants are similar to the ones mineral oil or metal steatite used in the conventional procedure, but also to new materials like polymer emulsions or polyamide dispersions. Also, the electrolytic phosphate conversion coating leads to a considerably shortened cycle time and a safer working environment.
Microporous Conversion Coating
The new microporous conversion coating produces a porous surface layer. Liquid lubricants are trapped in the many pores, which act as a porous sponge-like coating. The layer thickness of this conversion coating typically varies between 1 μm and 5 μm. The friction coefficient is as low as in the conventional lubrication system, which makes it a good alternative.
Single-Bath Lubrication
Developed initially by Toyota, this coating procedure is the most promising. It is environmentally friendly, eliminates all drawbacks of conventional zinc phosphating, and shortens the cycle time significantly. After shot blasting and hot water rinsing, the slugs are dipped into an aqueous bath that can contain water-based compounds with fatty acids, phosphates, polymer-based dispersants, salt, and wax. During cold forging, the heat generated by the deformation and friction results in a chemical reaction between the steel slug surface and the lubricant film, which forms a lubricating film boundary composed of zinc and sulfur.
Dual-Bath Lubrication
The dual bath lubrication system consists of a base coating adhered to the workpiece surface and a second layer of overcoating which reduces friction.
The Best Alternative?
The polymer coating process consists of four fully robotized steps that can be directly incorporated into the forging line. After the metal slug surfaces have been shot blasted and rinsed with warm water, they are immersed in a tank with water, wax, soap, and polymer. After coating, the workpieces are dried with warm air and are ready for the cold forging process.
The polymer coating is suitable for any single-stage or multi-stage cold forging lines. As the deformation of the workpiece increases, the control parameters will necessarily become more stringent. Therefore, a qualified workforce with extensive experience in manufacturing can benefit from this new procedure. Compared to the old bonderizing lines, the new polymer coating lines require different main parameters.
The benefits of polymer coating include:
- Environmentally Friendly
- There are no heavy metals, no sludge, and no hazardous waste, making it a perfectly safe tribological system for both workforce and the global environment.
- Leaner Process
- The cycle time is shortened up to 35 minutes, which leads to a significant increase in the line’s capacity, and thus the forging capacity of the shop.
- Cost Reductions
- The total cost of the coating process is reduced (lower energy and water consumption, no costly treatment of wastes.)
- Minimized WIP
- The polymer coating is a dry process, sensitive to moisture. Therefore, the coated slugs must be forged in a strictly defined time period, which helps to reduce work-in-progress (WIP.)
- Easier Machining
- The polymer coating is much easier to manage during the subsequent machining operations, either in sequence or by the customer. The conventional coating will produce a lot of dust during turning and machining.
Why Invest in Polymer Coating?
Farinia, a French forging manufacturer, is a good example of how to improve the cold forging process by investing in a polymer coating line. This is still a new approach in the cold extrusion process sector, and Farinia is always looking for ways to improve the operational performance of its forging plans.
The investment in the new lubricant coating system can be fully compensated by significant, overall improvements in the entire cold forging process: 15 metric tons of zinc were saved, while water and energy costs were minimized significantly. Farinia’s investment was supported by Agence de l`Eau, the primary authority for water management in France.
Cold-forged parts are highly valued in automaking and precision parts manufacturing. They can be manufactured with accuracy in large batches, with cost savings, and deliver excellent performance. Cold forging is one of the oldest and most widely adopted metal-forming techniques. With modern coating processes, it can be considered a good environmental option that doesn’t require any heating and has complete material usage. In addition, the globalization of industrial production and the rising demands for environmentally friendly solutions have increased competition in cold forging production.
But, cold versus hot forging, and their benefits or drawbacks, are no longer the only options for manufacturers looking for the best manufacturing option. Synergies between different processes and tools, and especially additive manufacturing, have forced the cold forging industry to look for better solutions and solve as soon as possible the issue with the zinc-phosphate lubrication system and its hazardous waste.
Therefore, resourceful manufacturers are developing alternative lubrication processes using polymer coating. Polymer coating is an environmentally friendly process that can promote leaner manufacturing, reduce operating costs and inventories, and improve profitability.
Ralitsa Peycheva is a technical writer on topics related to forging and casting techniques, the latest machinery, and tools. Follow her work at twitter.com/RPeycheva
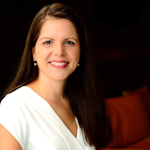
Ralitsa Peycheva | Web Content Specialist (Self-employed)
Ralitsa Peycheva is a technical writer on topics related to forging and casting techniques and the latest machinery and tools. Previously, she was a technical content manager for Mobility Work, a developer of computerized maintenance management systems for industrial operations.