We spoke with H. James Henning, the now-retired director of technology for the Forging Industry Association about how to calculate reduction on rings and sleeves for cast structures.
FM: Is there a specific formula to calculate reduction on rings and sleeves (rings drawn out on a pin)? I understand the way to calculate reduction on rings is to divide the wall thickness of the disc when it is punched by the wall thickness of the finished ring (for example, wall thickness is 10 in. when punched, and 4 in. when finished): The reduction is 2.5-to-1. Is this correct? Is there an additional factor if this ring is drawn out on a pin to gain length?
HJH: The wall-reduction levels in terms of percent reduction from start to finish are fairly straightforward. In that regard, you are basically correct.
However, total reductions are another matter. You have the pot die (used for most hollow blanks for rings). Assuming you are starting with a cast ingot/billet, the reduction is a function of the backward extrusion reduction followed by the subsequent reduction you described. However, the most important reductions are those obtained in final forging, because that's what controls the grain size of most steels.
The grain size reduces upon annealing if the final forging temperatures are proper for the alloy. For example, overheating can occur at only 2,200°F for low-alloy steel if there's little or no reduction. For austenitic stainless, the final grain size is controlled almost entirely by the final forging reduction.
The reduction requirements for cast material are important to consider because any remaining cast structures in the resulting billet can compromise the properties and leave residual porosity. However, when starting with press-forged billets (ahead of your ring forging), the reductions should have been sufficient by the method you described.
Guidelines and recommendations offered in this column are based on information believed to be reliable and are supplied in good faith but without guarantee. Operational conditions that exist in individual plants and facilities vary widely. Users of this information should adapt it, and always exercise independent discretion in establishing plant or facility operating practice.
About H. James Henning
For more than 40 years, H. James Henning held key technical positions in the forging industry, including as director of technology for the Forging Industry Association, and as president of Henning Education Services, a Columbus, OH firm specializing in customized education and training in forging technologies.
About the Author
Robert Brooks | Editor-in-Chief, Forging Magazine
The Editor-in-Chief of American Machinist, Foundry Magazine, and Forging Magazine, Robert Brooks has been a B2B reporter, writer, editor, and columnist for more than 20 years, specializing in the primary metal and basic manufacturing industries. His work has covered a wide range of topics including process technology, resource development, material selection, product design, workforce development, and industrial market strategies, among others.
Currently, he specializes in subjects related to metal components and product design, development, and manufacturing—including castings, forgings, machined parts, and fabrications.
Brooks is a graduate of Kenyon College (B.A. English, Political Science) and Emory University (M.A. English.)
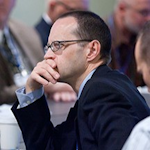
Robert Brooks | Editor/Content Director - Endeavor Business Media
Robert Brooks has been a business-to-business reporter, writer, editor, and columnist for more than 20 years, specializing in the primary metal and basic manufacturing industries. His work has covered a wide range of topics including process technology, resource development, material selection, product design, workforce development, and industrial market strategies, among others.
Currently, he specializes in subjects related to metal component and product design, development, and manufacturing—including castings, forgings, machined parts, and fabrications.
Brooks is a graduate of Kenyon College (B.A. English, Political Science) and Emory University (M.A. English.)