Pushing Freeform Optical Manufacturing to New Heights
Part Geometry
Through the support of US Navy Phase I and Phase II SBIRs, Optimax has significantly advanced its ability to manufacture and measure extreme freeform geometries. The most recent shape was designed with an aerodynamic conformal sensor window in mind. The outer dimensions of the finished part will be 585 x 480 x 195 mm, with 170 mm of concave (CC) sag, and deviation from a best fit sphere of over 400 mm. Placing this part firmly in the category of extreme freeform shapes; a shape that possesses a deviation from a best fit sphere that is on the same order as the size of the part. A rendering of what the finished part will look like is shown in Figure 1.
Polishing Platform
This part is approximately four times the size of the next largest freeform part ever manufactured at Optimax, and so required that a scaled-up robotic polishing platform be designed and built to accommodate it. This platform utilizes a 6-axis pick-and-place robotic arm for its motion and custom software and tooling to polish and figure correct the surface. Modular interfaces for tooling and for part holding exist on the arm and the base respectively, making the platform very flexible. Specialized tooling has been designed for targeting specific errors, working with specialized materials, and correcting axisymmetric and non-symmetric part geometries.
Download this article in pdf format.
The base was designed with the assistance of software that modeled the working volume of the arm to ensure the full aperture of both sides of the part could be reached. This software also enables testing of toolpaths prior to running, which is of special importance due to the high likelihood of collision between the arm joints, the part, the tooling, the shielding or a combination of any of these. A visualization of the platform running a toolpath validation prior to a physical polishing run is shown in Figure 2.
Challenges
Logistically, moving the part around a shop floor is challenging. The part is too big to fit into a standard parts tray and is too heavy to lift (weighing around 120 pounds), even with two people. Optimax’s solution to this problem was to use a cart-mounted crane as a part carrier and lifting mechanism. Specialized lifting fixtures were designed for both the CC and CX sides of the part to ensure the safety of the part and the operator during loading/unloading and in transit. Due to the size and cumbersome nature of the cart the polishing platform, generating platform, and metrology are located very close to one another.
The only reliable metrology option for this component is the coordinate measurement machine (CMM) due to the size and complexity of the shape. This is a tactile measurement method that compares discrete points taken from the part surface to the nominal shape of the part. Custom written code then calculates and displays the deviation values for each programmed point on the surface for use in creating new toolpaths.
Due to the tactile nature of the CMM measurement, it is difficult to gather meaningful data quickly. A typical measurement cycle takes several hours; slowing the iterative loop of figure correction and measurement, and lengthening the manufacturing schedule. For this reason, Optimax is actively developing a technology to reduce measurement time by two orders of magnitude. This technology is known as fringe reflection, or deflectometry, and utilizes an LCD screen and camera to calculate surface slopes[1]. Slope data is then used to calculate mid-spatial frequency error. Most recent data shows resolvability to 50 nm .
Additional challenges faced during this development include: achieving high enough material removal rates for reliable measurements and the inadequacy of best-fitting for monitoring figure error.
Download this article in pdf format.
Conclusion
As freeform optical components increase in size and complexity, so do the challenges associated with their manufacture. Trivial aspects of smaller components, such as movement and measurement time, become difficult and time-consuming. This presentation will discuss some of the solutions that Optimax developed to tackle the challenges involved with manufacturing large, extreme freeform optical components.
References
[1] M. Knauer et al., “Phase Measuring Deflectometry: a new approach to measure specular freeform surfaces”, Proc. SPIE 5457,366 -376 (2004).
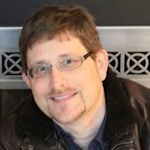
Todd Blalock | R&D Engineer, Optimax Systems, Inc.
A multi-disciplined optics/photonics engineer and entrepreneur with 20+ years experience and proven track record in product development, research, and intellectual property and patent generation with applicable skills in optics, electronics, and software development.
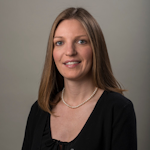
Jessica DeGroote Nelson | Director of Technology and Strategy, Optimax Systems, Inc.
Passionate about optical materials, fabrication, and testing processes, and how they can enable optical designers' dream designs to become reality.