Some forgers may see additive manufacturing as a competitive threat to their forming operations, but let’s consider also the possibilities that AM (or 3D printing) offers: To produce lightweight, compact spraying heads for forging dies, SMS group is 3D printing fixtures that are customized to the particular requirements and conditions of the respective dies.
These individual spray heads are capable of fast and flexible activation, and they produce a fine mist that is homogeneously distributed across the die surface. The cooling and lubricating effect of this shortens press cycle times and prolongs the service life of the dies.
As background, understand that spray heads are installed in closed-die forging presses to remove scale from the dies between the individual press strokes: the spraying process also cools, lubricates, and dries the die surface. But, conventionally manufactured spray heads reach a maximum effectiveness fairly quickly and must be replaced frequently.
3D-printed spray heads for forging dies are lighter; optimized to the needs of die spraying; and easier to handle, install, and replace.
SMS group designs and manufactures forging presses of various types, which prompted the decision to manufacture the spray heads using 3D printing. The starting material is a fine, polyamide-based powder that the developer reports produces a spray head structure that is 90% lighter than an identical part cast in steel. This improvement speeds up handling and placement/replacement of the spraying heads, which also adds to process efficiency.
SMS offers linear, cam-controlled, or servo-motor-driven die-spraying systems and industrial robots. The 3DP spray heads add to this line of products. In service, they shorten the non-productive time of the press, so press output may increase.
More than this, 3D printing offers greater flexibility to the SMS engineers designing the presses and the spray heads. They are able to arrange the individual nozzles exactly according to the customers’ requirements, even giving each nozzle a unique shape as may be indicated by the operating program.
There are new options for actuating the 3DP spray heads, too. Each nozzle can be actuated separately, for spraying and for separately blowing out atomizer air, either simultaneously or offset in time. Consuming the minimal volume of a spray medium (die lubricant, for example), the heads produce a spray pattern that is homogeneously distributed over the tool surface. Individualized designs help to prolong the service of the die.
Due to their unitary structure, 3DP spray heads can be used at pressures between three and more than 10 bars, and are able to generate different spray patterns.
The new 3DP spray heads may be installed in new presses, but also are well suited for retrofitting to existing forging presses. SMS noted that it designs all 3DP spray heads via a highly automated sequence, so it can manufacture the parts quickly. This means that customized 3DP spray heads can be developed and delivered on short notice.
According to the developer, 3D printing offers the system engineers a chance to apply an alternative to the laminar pattern that is standard for die spraying. The perforated structure prevents spray medium from accumulating on the spray head. The individual, interior channels are flow-optimized, which precludes deposit formation. Furthermore, as 3DP spray heads have no parting lines, the spray medium is not exposed to air during downtimes and cannot dry out.
Drawing on the design example of the previously developed disk spray heads, SMS group engineers adopted the external-mix two-component nozzle design that produces an extremely fine aerosol. In contrast to internal-mix systems, segregation of the individual components cannot occur with this technology.
To change the nozzles, SMS group continues to use for the proven membrane material employed for disk spray heads. The membrane platelets are located directly at the nozzle. Quick replacement time minimizes dripping and contributes to overall efficiency and system availability.
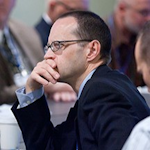
Robert Brooks | Editor/Content Director - Endeavor Business Media
Robert Brooks has been a business-to-business reporter, writer, editor, and columnist for more than 20 years, specializing in the primary metal and basic manufacturing industries. His work has covered a wide range of topics including process technology, resource development, material selection, product design, workforce development, and industrial market strategies, among others.
Currently, he specializes in subjects related to metal component and product design, development, and manufacturing—including castings, forgings, machined parts, and fabrications.
Brooks is a graduate of Kenyon College (B.A. English, Political Science) and Emory University (M.A. English.)