Concept Integrates Metal Production and 3DP in Industrial-Scale Plant
SMS group, the designer and builder of forging presses, ring-rolling mills, and thermal processing systems, is in partnership now with a metal 3D printing systems supplier to co-develop and market an industrial-scale process for additive manufacturing systems to produce metallic components. Additive Industries, the Netherlands-based partner in the new venture, is the originator of the 3D printing package, called MetalFAB1. Introduced two years ago, the developers claimed this system “offers substantially improved performance over typical midrange (additive manufacturing) systems,” and promised significant increases in finished-part reproducibility, process productivity, and system flexibility.
MetalFAB1 was beta-tested and later adopted by Airbus for production of aerospace parts. Other manufacturers have applied MetalFAB1 to produce parts used in robotics, mechanical engineering, automotive, and medical technology systems.
The partners have not indicated the value or organizational structure of their venture. They intend to set up a “Democenter” at the SMS location in in Mönchengladbach, Germany, in the coming months. It will include an Additive Industries MetalFAB1 printer installed next to a pilot-scale metal-powder plant, and the two processes working together.
The laser-based MetalFAB1 metal powder bed fusion process is carried out in a modular system designed for customizable configurability for operators and/or applications. It has multiple, large build envelopes (420x420x400 mm) with individual, integrated powder handling. Reportedly, MetalFAB1 was the first industrial 3D printer able to combine up to four materials simultaneously in a single machine.
MetalFAB1 can be equipped with a maximum of four full-field lasers, so there is no need for “stitching” together separately printed parts of large objects. The system includes an integrated furnace for heat-treatment of the printed parts.
More than a developer of forging operations, SMS is an engineering group focused on metallurgical processes and plant technology. In its announcement, SMS noted its contribution to the alliance is expertise in manufacturing of metal powder. “As one of the world’s leading machine and plant builders for the metallurgical industry, we have extensive design know-how and process engineering expertise in the field of vacuum melting plants. We are now transferring this expertise to powder production plants,” stated Norbert Gober, SMS group vice president for Research and Development.
Their process design is premised on linking the powder manufacturing and 3D printing processes. But, concept will encompass other manufacturing stages, up to delivery of the finished parts. “The entire process is designed for maximum productivity, with the result that additive manufacturing can finally enjoy competitive success in serial production,” stated Guido Kleinschmidt, an SMS group board member.
Starting from the production of metallic powders, the process calls for alloys to be induction-melted under vacuum in a crucible. Then, the liquid metal is atomized using pure argon in an oxygen-free atmosphere. “The quality of the powder manufactured is crucial for the quality of the finished product. To enable us to make faster progress in powder production, we are building an industrial-scale pilot system, which is scheduled to go live at the end of the year,” stated Markus Hüllen, v.p. of the SMS group 3D Competence Center.
Next comes the MetalFAB1 printing process. After additively manufacturing the parts, the build plate with parts is directed a heat treatment furnace (developed by SMS Elotherm), for a stress relief cycle. Then, the parts are transferred via robot into storage.
The MetalFAB1 system is designed to run autonomously, around the clock, for low-cost high productivity.
Once formed and finish machined, the parts are ready for shipment to manufacturing customers.
“Five years ago, we started with the development of the world’s first 3D metal printer for high-end production applications. Today, with our MetalFAB1, we are accelerating industrial additive manufacturing as one of the industry’s leading technology suppliers,” observed Daan A.J. Kersten, CEO of Additive Industries. “In SMS group, we have found a partner who has experience in planning production complexes such as these and delivering them on a turnkey basis.”
According to Gober, the upcoming Democenter “will allow us to align the powder plant with its process guidance system perfectly with the printer and its parameters. We will then be able to apply this practical experience on an industrial scale, and offer this as a turnkey solution to high-end users.”
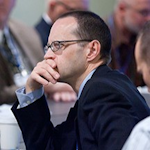
Robert Brooks | Editor/Content Director - Endeavor Business Media
Robert Brooks has been a business-to-business reporter, writer, editor, and columnist for more than 20 years, specializing in the primary metal and basic manufacturing industries. His work has covered a wide range of topics including process technology, resource development, material selection, product design, workforce development, and industrial market strategies, among others.
Currently, he specializes in subjects related to metal component and product design, development, and manufacturing—including castings, forgings, machined parts, and fabrications.
Brooks is a graduate of Kenyon College (B.A. English, Political Science) and Emory University (M.A. English.)