SMS group revealed details of a new ring-rolling concept it has developed, which will be installed for the first time this year in a machine for Forgia Rapida, at its plant in Bologna, Italy. The RAW 100/80-3000/480 ecompact® radial-axial ring rolling machine will be installed this summer and start producing rings in September.
As detailed by the developer the machine design centers on electro-hydraulic direct drives that are mounted on the roll shafts, a new approach to drive systems for ring rolling, which SMS contends can reduce energy consumption by up to 40% compared to conventional ring-rolling machines.
The RAW ecompact for Forgia Rapida will replace a smaller machine in operation at Bologna, and will roll rings with diameters up to 3,000 mm and a maximum height of 480 mm. The radial rolling force will be 1,000 kN and the axial force up to 800 kN.
Forgia Rapida will use the machine produce rings for radial compressors, reciprocating piston compressors, and gas turbines. It currently produces around 4,000 metric tons per year of forgings.
Short delivery times and fast construction and commissioning are essential elements of the new machine concept, SMS noted. Rings with standardized dimensions can be used for testing and verifying the performance parameters, and rings sizes currently in production can be used. “The cost-benefit ratio of this new development has really impressed us,” stated Lorenzo Badini, owner of Forgia Rapida. “We are convinced that it will pay back shortly. ”
SMS contends that investment costs for the RAW ecompact are about 20% lower than for conventional ring rolling machines. The fact that it does not require a central hydraulic system means there is no associated machine and foundation pipework to be installed. This also eliminates the environmental risk of oil leakage.
The developer added that the RAW ecompact is mounted on a simpler foundation than conventional ring rolling machines, and requires no additional space for a separate hydraulic power system.
The lack of hydraulics reduces energy consumption and maintenance costs, and also reduces operating noise. “We no longer have a complex oil circuit, but just compact electric drives – and for that we need no more than two cables,” stated Robert Düser, SMS group sales manager, Ring and Wheel Rolling.
SMS group will develop RAW ecompact machines in various sizes: the largest has been designed to produce rings with a maximum outside diameter of 3,600 mm, with horizontal unloading.
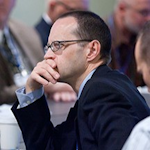
Robert Brooks | Editor/Content Director - Endeavor Business Media
Robert Brooks has been a business-to-business reporter, writer, editor, and columnist for more than 20 years, specializing in the primary metal and basic manufacturing industries. His work has covered a wide range of topics including process technology, resource development, material selection, product design, workforce development, and industrial market strategies, among others.
Currently, he specializes in subjects related to metal component and product design, development, and manufacturing—including castings, forgings, machined parts, and fabrications.
Brooks is a graduate of Kenyon College (B.A. English, Political Science) and Emory University (M.A. English.)