World Day for Safety and Health at Work (April 28) was held to promote discussions about occupational safety and health (OSH) around the world.
Here Claudia Jarrett, U.S. country manager at automation parts supplier EU Automation, explains why Industry 4.0 and key performance indicators (KPIs) are crucial to establishing a positive working culture in manufacturing environments.
Captain Scott Kelly once said, “safety has to be everyone’s responsibility.”
“Everyone needs to know that they are empowered to speak up if there’s an issue.”
Kelly’s observation also applies to manufacturing environments. Aside from the obvious need to protect employees’ well-being, OSH is integral to a good working culture in modern manufacturing environments.
In contrast, CNN reports that 44% of young adults aged 20 to 35 find a career in oil and gas unappealing because they think the industry is dangerous. There's a growing awareness of the importance of safety which is why financial officers (CFOs) interviewed in PwC’s 2020 CFO Pulse Survey said tech spending on health and safety measures had risen to 8.6% that year, up from 5.3% in the comparable period before the COVID-19 pandemic.
Despite this, manufacturers must do more—especially in environments with hazardous machinery.
Each year, physical contact with machines and powered equipment still accounts for a significant number of life-altering injuries for workers. In the United States, 1,972 machine guarding violations were cited in 2018 alone, and a common infraction was failing to implement effective machine guarding.
How can accidents be minimized? Industry 4.0 and digitalization hold the key.
Prominent examples include the large manufacturer Ericsson, which has equipped the frontline workforce with connected hardhats giving on-demand, voice-controlled access information including safety protocols.
Despite this positive example, many manufacturers face obstacles when implementing hardware and software to go digital, such as misjudging the scale of rollout or failing to set specific, measurable, relevant, and achievable key performance indicators (KPIs).
Lack of experience and training among workers can also be an issue. Let’s look at how manufacturers can overcome these obstacles, and why making safety everyone’s responsibility might be the best solution.
Learning Fast
Automation hardware and software are already shown to improve worker safety. Indeed, traditional six-axis robots were first deployed on production lines in the 1960s to remove the presence of workers from some aspects of the production line.
According to PwC’s Digital Factories 2020 report, “Robots and other digital technologies will also make workers’ lives in the factory easier, safer and more efficient.”
Greater levels of safety will be made possible through automation combined with artificial intelligence (AI) and machine learning (ML). ML describes a type of AI that allows software algorithms to learn and develop while the equipment is in operation.
Take the example of machine safety devices, such as automated safety curtains or automated kill switches, which can also be used in conjunction with a safety programmable logic controller (PLC). The PLC retrieves data from automated machines, light sensors, and other data from other sensors on the factory floor, and controls whether an alarm should be raised based on a detected hazard.
For instance, when an operator walks into the perimeter of an industrial robot, the PLC can use data from the safeguarding sensors and correlate this with real-time data, which shows the robot is currently working at high speeds. At this point, the PLC stops the robot automatically and raises the alarm.
With AI and ML, industrial IT systems can search through manufacturing data to highlight dangerous processes as part of a wider overall safety strategy. By combining ML with a Supervisory Control and Data Acquisition (SCADA) platform, a manufacturer could identify if a piece of equipment is repeatably exhibiting safety issues.
Software is also becoming more flexible and customizable to give manufacturers the information they want when they need it. ML software can help robotic systems adapt to their work environments rather than designing every aspect of the environment and processes to suit the limitations of the machines, as in previous decades.
These advances will enhance both productivity and safety, and subsequently lead to more applications involving true collaboration between robots and humans.
Human Touch
Even with Industry 4.0 technologies in place, the importance of human workers in OSH shouldn’t be underestimated. McKinsey and Company cite the example of a chemical producer that closed down a factory that ranked lowest in safety because it believed that the culture of the plant was irreparable.
Three weeks were allowed to revamp the plant’s operating processes, fix high-priority safety defects and provide essential training. Three months later, reports McKinsey, “...the factory had significantly improved its profitability and injuries were virtually nonexistent.”
This example shows why it is so important that senior managers are supportive of safe and healthy work practices. Indeed, McKinsey recommends that “organizations can take a ‘managed safety’ (as opposed to ‘regulated safety’) approach.”
Its report advises that “management can trust employees to use their own judgment in instances when strict compliance with safety rules either wouldn’t be enough to ensure safety or could introduce risk.”
This brings us to human empowerment or, as Captain Kelly put it, “Everyone needs to know that they are empowered to speak up if there’s an issue.”
To encourage the human-empowering approach to safety, it’s important for leaders to provide positive feedback to teams that take it upon themselves to improve safety. To this end, Industry 4.0 and digitalization will be vital for getting workers involved.
Effective digitalized OSH strategies will depend on more accessible data shared through customized reports, and less skill-intensive control through easy-to-use human-machine interfaces (HMIs). The results are improved data management and sharing, reporting, communication, and achievement of KPIs.
But why are specific, measurable, relevant, and achievable KPIs so important to an effective digitalized safety strategy?
A study by Slovenia’s University of Maribor, Key Performance Indicators and Industry 4.0 – A Socially Responsible Perspective, put it best: “The benefits of KPI implementation […] would be the basis for achieving a higher level of productivity and establishing a reward system or rewarding the performance of employees, which would have a positive impact on the motivation and commitment of employees.”
The report adds that “Success of Industry 4.0 depends critically on employees and other business partners, not only on equipment.”
Let’s return to our example of an operator combining ML with the SCADA platform to identify if a piece of equipment is repeatably exhibiting safety issues. The operator can then supervise KPIs and communicate these throughout the factory.
Here, Industry 4.0 technologies, like sensors, can play a crucial role―especially as part of a low-cost digital retrofitting strategy.
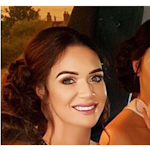
Claudia Jarrett | Head of Sales - The Americas, EU Automation
Claudia Jarrett is the Head of Sales for The Americas at EU Automation. EU Automation stocks and sells new, used, refurbished, and obsolete industrial automation spares. Its global network of preferred partner warehouses and wholly owned distribution centers enables it to offer a unique service within the automation industry, spanning the entire globe. It provides worldwide express delivery on all products meaning it can supply any part, to any destination, at very short notice.