A forged part may be described as ‘precise’ or ‘near-net shape’, but it’s never finished unless its trimmed or surface-treated, or especially, machined. The scope of machining is itself a vast subject, but from the perspective of forging operations it is a final, value-adding step to the main production process. Whether the forged parts are wheels, gears, turbine blades, or large structural elements, the finish machining has to be reliable and efficient.
Depending on the types of forgings being machined, the operation has to be capable of flexible set-ups and/or high throughput. Most important, it has to be complete the task set out from the start of the forging process: achieving high-quality surface finishes and dimensional precision.
Vertical turning has emerged as a particularly effective machining strategy for forgers with high-volume production requirements. In particular, operations producing gears and automotive parts need systems for consistent machining of complex, precision parts. One source of vertical lathe systems, EMAG LLC, recently introduced several new designs that meet the standard, including the VM 9 vertical turning center. This latest system in the VM series is designed to machine chucked components with a maximum diameter up to 450 mm. It features a tool turret that can be set-up with twelve tool positions and can be equipped with driven tools to carry out drilling or milling operations. An integrated probe performs continuous quality control, ensuring process reliability.
Also introduced recently was the EMAG’s VL series, a “modular inverted vertical lathe design.” Each of the four machines in the series are described as compact designs — small-footprint machines are important to plants installing additional capability, where extra floor space is not always available — that are adaptable to medium- and large-batch runs. The VL machines also have an integrated automation system for transporting workpieces, which works together with self-loading pick-up spindles to reduce machine cycle times and promote higher throughput.
VL machines are arranged with all systems (electrics, hydraulics, cooling system, cooling lubricant and central lubrication system) easily accessible for operation and maintenance requirements.
For many machining operations, including those installed to complete forging processes, precision (not high-throughput) is the primary design objective. In shops and plants finishing wheels or hubs, or gears or shafts, the complexity of a design and the appearance of the finished part are essential factors in the selection of a cutting, turning, or grinding machine.
The Präwema SynchroFine 205 HS gear-honing machine, now available from German Machine Tools of America, has a direct-drive, digitally controlled spindle design that achieves precise, rigid synchronization for the tool and the workpiece. The supplier maintains that the Präwema Honing gear finishing process produces quality comparable to grinding for spur and helical gears, as well as shafts.
Part of the machine’s precision is software-based, with programming that checks the stock allowance and workpiece run-out, and then optimizes the X-axis approach distance. Measuring the workpiece does not affect the cycle time and that process can reduce cycle times overall by 3 to 5 seconds, according to GMTA.
The machine features a pick-up design that addresses many operations’ desire for automating machining or finishing. The workpieces and dressing tools are loaded and unloaded by the workpiece spindle. The large X-axis travel enables placement of additional stations adjacent to the loading/unloading station inside the machine, such as a two-flank roll-checking device. Robots and conveyor systems can be integrated to the operation.
GMTA builds the machine on a natural granite bed to promote stability and control thermal fluctuations. The X and Z axes are equipped with linear motor drives. The cutting tool is clamped with a hydraulically operated system and the tool spindle can be swiveled into a vertical position, enabling easy access.
The Präwema SynchroFine 205 HS-D model, equipped with two spindles, is offered for further reduction of cycle times. And, the developer offers additional options for machining oversized drive shafts up to 850 mm long.
Machining automotive or commercial vehicle wheels is a function that requires set-up flexibility, reliable throughput, and precision. The new You Ji YV-600E2T vertical turning center available from Absolute Machine Tools is designed for high-volume machining of large aluminum wheels (or similar products.) The compact design can operate as a standalone workcell, or can be integrated with other machines to form a heavy-duty, yet flexible manufacturing system.
The VTC’s maximum swing is 33.4 in. and the maximum turning diameter is 29.5 in. The rigid vertical column and base are Meehanite iron castings, heavily ribbed to reduce thermal distortion and vibration dampening. Its X and Z axes have roller-type linear guideways.
The heavy-duty spindle incorporates double roller bearings as well as 45-degree angular contact thrust bearings. The spindle is also protected from coolant contamination; NN-type spindle bearings are used to withstand high centrifugal loads as well as high spindle loads. The 100-HP high-torque spindle motor drives the spindle via belts, providing plenty of power for heavy-duty machining and the high speeds necessary for fine finishing.
Some automotive forgings, like gears and shafts, require high-precision machining. The Junker Group, which designs various grinding machines, last year expanded its portfolio to include non-cylindrical grinding of camshafts, in low-to-medium lot sizes. By using up to two high-performance grinding spindles, bearings journals and cam lobes can be rough and finish ground in a single clamping set-up. High-powered grinding spindles, together with high-hardness tooling (e.g., CBN grinding), promote high removal rates and performance standards.
The Junker Lean Selection cam machine is capable of grinding all cam lobe profiles and geometries at high-speed – from concave to elliptical – and is suitable for manufacturing everything from prototypes to large production runs.
Machining is becoming an increasingly important process stage for many forging operations, and while the priorities for each one will vary according to their product design, material, and volume, the objective in each case is the same: to extend the value designed into the forging into the new stage of production, to ensure forging buyers gain the precision design they have ordered.
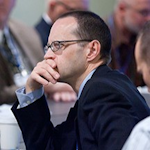
Robert Brooks | Editor/Content Director - Endeavor Business Media
Robert Brooks has been a business-to-business reporter, writer, editor, and columnist for more than 20 years, specializing in the primary metal and basic manufacturing industries. His work has covered a wide range of topics including process technology, resource development, material selection, product design, workforce development, and industrial market strategies, among others.
Currently, he specializes in subjects related to metal component and product design, development, and manufacturing—including castings, forgings, machined parts, and fabrications.
Brooks is a graduate of Kenyon College (B.A. English, Political Science) and Emory University (M.A. English.)