Metal Technology Inc. in Albany, OR, recently reported it has achieved “production readiness” on a new forging line.
“By coupling our computer-controlled, 1,200-ton hydraulic press with our new multi-station digital rotary-hearth furnace, we are able to achieve some of the highest quality and repeatability levels in the industry,” according to Pat Coffey, v.p. – Operations. “We are able to tune our process by adjusting heat, tonnage, speed, and travel, programmatically allowing us to create a recipe that will yield the ideal microstructure for each application. This was an absolute must given the unique demands of the defense, scientific, and space exploration customer base we serve.”
MTI has multiple manufacturing capabilities in addition to forging, including deep-draw forming, spinning, CNC machining, and additive manufacturing. Its products are engineered parts in critical materials, including tantalum, niobium, zirconium, titanium, tungsten, Inconel, and molybdenum.
“Our new forging capability combined with our precision machine shop further strengthens MTI’s competitive position by allowing us to provide fully comprehensive end-to-end solutions for our customers,” according to CEO Gary Cosmer.
“We are now able to forge components to near net-shape with superior grain structure saving time and material due to our controlled forging process,” Cosmer continued. “We can then machine those components in house to final geometry and back it up with AS9100 level inspection using the most sophisticated precision measuring equipment in the industry to assure the highest quality standards.”
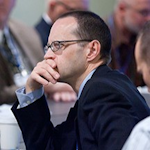
Robert Brooks | Editor/Content Director - Endeavor Business Media
Robert Brooks has been a business-to-business reporter, writer, editor, and columnist for more than 20 years, specializing in the primary metal and basic manufacturing industries. His work has covered a wide range of topics including process technology, resource development, material selection, product design, workforce development, and industrial market strategies, among others.
Currently, he specializes in subjects related to metal component and product design, development, and manufacturing—including castings, forgings, machined parts, and fabrications.
Brooks is a graduate of Kenyon College (B.A. English, Political Science) and Emory University (M.A. English.)