The months ahead will see a series of new forging concepts arrive at the commissioning stage, guided by advanced standards for process efficiency and product quality — as well as by forging buyers’ demands for precision components in more advanced materials.
Weber Metals in Paramount, CA, near Los Angeles is preparing to install the “the largest aerospace forging press in the Western Hemisphere, and the largest in the world installed with private investment.” The project long in development and described as a $170-million investment makes an impressive headline for a wave of projects signifying new forging operations and technologies.
The closed-die forging machine will be built by SMS Group under contract to Otto Fuchs KG, the German parent company to Weber Metals. The new machine will forge extra-large nickel- and titanium-based alloy parts for commercial aerospace contracts, including Airbus and Boeing projects.
According to SMS, its GUF4-type hydraulic press will be a "pit mounted" design capable of achieving forces of 540 MN (60,000 tons/in.2), with a 6,000X3,000-mm (236X118 in.) die clamping area and a stroke of 2,000 mm (79 in.)
SMS noted that steel castings produced for the four-column press will weigh up to 350 mt (386 tons.) The new machine will be structurally reinforced with four, forged tie rods, an integrated load-balancing feature that will allow the operators to forge parts to extremely tight tolerances.
New Concepts in Die Forging
“This large-scale investment underpins our strategic alignment in the global aerospace market,” stated Dr. Klaus Welschof, aerospace industry sales manager for Otto Fuchs.
Weber Metals has been a subsidiary of Otto Fuchs since 1978, producing open-die and closed-die forging in aluminum and titanium alloys, mainly for aerospace manufacturing, like aircraft fuselage and wing structures, as well as landing gears.
Presently, the plant operates four open-die presses (rated at 1,200 to 5,000 tons) and five closed-die machines (rated at 1,500 to 33,000 tons.)
SMS noted the new press would allow Otto Fuchs to expand its portfolio of “extra-large premium-grade forgings” into even larger dimensions, and introduce the possibility of converting large structural components to lighter materials.
Start-up for the new press is expected late in 2017.
Sooner, but still within the scope of forging for aerospace, will be the first of two, 8-MN isothermal forging systems that Leistritz Turbinentechnik GmbH ordered from Siempelkamp. The 8-MN system producing titanium aluminide turbine blades will start production at the Leistritz plant in Remscheid, Germany, in March. The second unit is set to start up in 2017.
According to Siempelkamp, Leistritz will use these forging presses to manufacture a new generation of aircraft engine parts, incorporating material that is 50% lighter than the nickel-base alloys now commonly used for turbofan aircraft engines, with comparable material strength as those alloys. The difference is intended to enhance aircraft fuel efficiency to a significant extent.
Titanium aluminide (TiAl) alloys are intermetallic chemical compound that are high in density, lightweight, and heat-resistant. The material’s ductility has been a problem for product designers though, one that has begun to be address by aerospace (and automotive) designers only in recent decades.Â
As detailed by Siempelkamp, TiAl’s intermetallic structure is the basis for its high strength and excellent creep resistance at high temperatures. That, as well as the material’s lightness (the density is 4 grams per cubic meter) make it well suited for aircraft engine components. The material provides the potential to reduce the weight of turbine blades for aircraft engines by up to 50%, according to the forging machinery developer; its strength-to-weight characteristics also provide a significant reduction of centrifugal forces within the aircraft engine. Naturally, a lighter aircraft engine design will contribute decisively to reduced fuel consumption.
Leistritz, which forges turbine components at Remscheid, has been a development partner to aircraft engine manufacturers for decades, helping to finalize designs in high-strength materials like high-temperature steels, titanium, and nickel-based alloys. It supplies turbine blades as forged blanks, or as finished structures ready for installation.
While intermetallic titanium aluminide had long been considered "unforgeable," Leistritz concludes that forging can initiate a re-crystallized structure that casting cannot achieve, one that is necessary for safety in rotating engine parts. In addition, forging offers higher process stability than casting, meaning the turbine blades conform to aircraft manufacturers’ very high quality requirements. Â
Leistritz has developed a forging process wherein blanks can be formed without cracks under carefully defined conditions at 1,150-1,300°C. The high forming temperature and the long dwell time of the forgings in the die, due to forming speeds of less than 0.1 mm/s, make it necessary to preheat the tools to forging temperature.Â
The extremely low press speeds require hydraulic drive control to be especially accurate and uniform. Special guide and sealing systems ensure uniform compression, thus avoiding the stick-slip effect.
The symmetrical press design, with a cross thread guide located on the outside, allows for high precision forging. Because the guide elements are isolated from the heat source there is no thermal influence on the guide.
The large distance between the guidance elements and the high rigidity of the press frame also contribute to precisely opposite aligned upper and lower dies during the forging process.Â
Leistritz has operated a Siempelkamp 50-MN isothermal forging press since 1984. Because of its satisfaction with that system, Leistritz contacted Siempelkamp to evaluate different process concepts for the new titanium aluminide blade production program.
During pilot production, engineering talks were started concerning the design of the new isothermal line. At the start of 2014 both companies cooperated to develop the requirement profile for the plant allowing, series operation.
In November 2014, Leistritz commissioned Siempelkamp to develop and build two manufacturing plants for series production of titanium aluminide turbine blades.
Because the molybdenum contained in the dies sublimates in open air at temperatures over 600°C, oxygen has to be prevented from entering the dies. Therefore, the entire plant will be enclosed, which allows a completely automatic process — from inserting of the blank at room temperature to unloading of the forged turbine blades — all within an inert gas atmosphere.    Â
Siempelkamp is supplying both presses from a single source. The scope of supply for both presses includes a rotary hearth furnace, a loading manipulator, the forging press, the tool heating system, the hydraulic drive system, and the complete electrical control package. Process controls will monitor and document all process parameters according to the certification standards in the aircraft industry.
New Concepts in Ring-Rolling
Rolling rings is a discrete segment of the forging industry – relying on common principles of forming technology but using speed as an additional force factor to produce rings with reliable structures and strength. Likewise, aerospace, energy, and other common consumer markets have guided new developments in ring-rolling technologies.
Recently SMS revealed a new radial-axial ring rolling machine it has developed, the RAW ecompact®, an order for which was placed by Forgia Rapida, Bologna, Italy. That plant currently produces around 4,000 mt per year of forgings.
Delivery for the RAW 100/80-3000/480 ecompact machine will take place this summer, with start-up scheduled in September.
The design is equipped with electro-hydraulic direct drives that are mounted on the roll shafts. This novel design can reduce energy consumption by up to 40% compared to conventional ring rolling, according to the developer.
At Forgia Rapida the RAW ecompact will replace a smaller ring-rolling machine, and will roll rings with diameters up to 3,000 mm and a maximum height of 480 mm. The radial rolling force will be 1,000 kN; the axial force up to 800 kN.
SMS noted the short delivery times and speedy construction and commissioning are essential elements of its new machine concept. Rings with standardized dimensions can be used for testing and verifying the performance parameters. In addition, rings from the current production stock can be used, which will ensure that the machine reaches its full performance capacity within a very short time.
“The cost-benefit ratio of this new development has really impressed us,” stated Lorenzo Badini, owner of Forgia Rapida. “We are convinced that it will pay back shortly. ”
According to SMS estimates, the investment costs for the RAW ecompact are 20% lower than for conventional ring rolling machines. In addition, because the design has no central hydraulic system means there is no machine and foundation pipework to be installed. This has apparent economic advantages, but it also eliminates the risk of environmental pollution by oil leakage, SMS noted.
The RAW ecompact is mounted on a simpler foundation than conventional ring rolling machines, and additional installation space for a separate hydraulic power pack is not required.
This fact also reduces operating costs in terms of energy consumption, as well because of “the almost complete elimination of hydraulic oil,” the developer explained. Operating noise levels also will be lowered significantly, according to SMS.
“We no longer have a complex oil circuit, but just compact electric drives, and for that we need no more than two cables,” according to Robert Düser, sales manager for SMS group’s Ring and Wheel Rolling. “This ring rolling machine is unique in the world.”
Reportedly, the RAW ecompact concept was developed in a period of about eight months. It is a fully automatic operation overseen by a CNC program. It will be supplied complete with the “CarWin” (Computer Aided Rolling under Windows) control software and the “RollTech Rings” technology software.
CarWin controls and automates the rolling process: After the target data for the rings to be produced has been entered, the software will evaluate all factors for credibility and conformity with the CNC system of the ring-rolling machine.
RollTech will simulate the ring rolling process in order to ensure “rollability” of the products, and generate all required process parameters. After the operating personnel enter the final ring geometry and the material data, RollTech will calculate the necessary machine settings according to stored process models. Together, the two programs allow ring manufacturers to reproduce any product that has ever been produced in the past, reliably and efficiently.
SMS noted it would build RAW ecompact machines in various sizes: The largest has been designed to produce rings with a maximum outside diameter of 3,600 mm, with horizontal unloading. The RAW ecompact for Forgia Rapida will produce rings for radial compressors, reciprocating piston compressors, and gas turbines, among others.
A recently unveiled Siempelkamp design combines open-die forging and ring rolling in a contiguous process. The forging press will start up in October at L’Union des Forgerons, in Méréville, France. The ring-rolling mill will be installed after that, and start up in the summer of 2017.
Siempelkamp’s combination brings together a 33/30-MN press to produce conventional open-die forgings weighing up to 10 metric tons, as well as ring blanks as feedstock for the ring-rolling mill. In total, the new line will allow the plant to achieve a level of flexibility for forming high-value materials for heavily engineered products
Forgerons aims to expand its capacity for nickel-based and titanium alloys, for products in high demand by aerospace manufacturers. The new press’s precision lifting and centering system will ensure high accuracy for blank punching and piercing.
The ring-rolling mill that processes the ring blanks will have radial and axial forces of 4,000 kN, each, for maximum ring diameter of 2,500 mm. The mill will roll rings up to 700 mm high and weighing up to 5 metric tons.
L’Union already produces forged parts and rolled rings in specialty and tool steels (particularly for pressurized vessels), stainless, and nonferrous alloys (aluminum, copper alloys, titanium). The current operation consists of several hammer mills in the 600- to 2,000-kg range, along with an open-die press and a circular rolling mill. A range of heat-treating options are offered, and finished products are available as-forged, sand blasted, rough machined or custom machined.
According to Michel Discour, president and director general of the forger near Paris, “We will be able to manufacture a higher number of difficult-to-form materials in the future that require higher pressing and rolling forces. This includes higher-quality materials, larger dimensions, and higher working weights.
“We will be able to achieve higher outputs,” he continued. “We specialize in the flexible manufacturing of complex products; the new machines will help in this regard because we will achieve shorter delivery times.”
In addition to the new open-die press and ring-rolling mill, Forgerons’ new line will have dedicated furnaces and material handling systems.
Siempelkamp will supply all the mechanical equipment for the forging press and the ring-rolling machine. For the latter, it also will provide the hydraulic system, electrical system, the process controls and the rolling dies.
Oilgear Towler will contribute the hydraulic and electrical systems for the open-die press. Glama will supply the charging manipulator, the forging manipulator, and a rail-bound forging robot that will transfer ring blanks from the press to ring-rolling mill.
According to the developer, the ring-rolling mill’s “Universal Cassette Design” makes it possible for the forger to use different main roll configurations in the same machine to increase flexibility and throughput, even for small batches, because the cassette can be exchanged within 30-50 minutes.
Siempelkamp’s SicoRoll 2.0 control software was specially developed for ring-rolling operations, and recently was updated with new features for greater precision in process control. Stored rolling models will help Forgerons during process planning. Process simulation programs take into account the machine’s threshold values, so all relevant rolling parameters are determined.
The SicoRoll program uses a database that stores the tool and material data, and it contains the standard rolling curves and strategies as the basis for the planning process. The calculated rolling parameters are transmitted to the machine control, which ensures the optimal ring rolling process and keeps the rolling parameters synchronized with the process.
During rolling, two lasers measure ring dimensions on a constant bases, and product temperature is monitored online. Siempelkamp describes temperature-data feedback as “an integral part” of the updated SicoRoll 2.0 software control.
The software also simulates ring blank dimensions for the forging press.
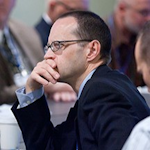
Robert Brooks | Editor/Content Director - Endeavor Business Media
Robert Brooks has been a business-to-business reporter, writer, editor, and columnist for more than 20 years, specializing in the primary metal and basic manufacturing industries. His work has covered a wide range of topics including process technology, resource development, material selection, product design, workforce development, and industrial market strategies, among others.
Currently, he specializes in subjects related to metal component and product design, development, and manufacturing—including castings, forgings, machined parts, and fabrications.
Brooks is a graduate of Kenyon College (B.A. English, Political Science) and Emory University (M.A. English.)