The productivity benefits of robotics have been well documented.
Cebr, a UK-based economic forecasting and analysis firm, released a robotics report on March 15 that showed robotics investment has contributed to about 10% of GDP per capita growth in OECD countries from 1993 to 2016.
But as plants become more automated, worker health and safety may increase, as well. That's because robotics can perform repetitive motions that often lead to injuries, fatigue and quality issues.
"The deburring, or part-finishing, process is an example of a task that is becoming less risky and more productive through the use of automation," says Robert Little, CEO of ATI Industrial Automation, a manufacturer of robotic accessories and robotic arm tooling. "If you think about using a deburring tool to repetitively work on parts, it takes a physical toll on you," Little says. "In addition, the tools you use can be dangerous. If you're not paying attention, you can injure yourself quite easily. So it makes complete sense that robots would go into this field to try to make it safer and reduce the health risks that could occur because of it."
Minimizing Defects
Traditionally, deburring and material removal have been manual operations because automated tools had limited capabilities. Little explains that robots are not inherently repeatable or accurate.
"For example, conventional automated deburring tools can perform adequately along a straight edge or surface, but these tools ultimately fail when part tolerances or paths are not exact," Little says. "Deburring tools must have some forgiveness, or compliance, built in to compensate for this lack of repeatability. They must have the ability to physically move when they make contact with the part so it produces a constant force. This reduces or prevents the robot from exerting excessive force on the part, which can cause defects."
iA-Robotics, a Murrieta, Calif., provider of global robotics automation solutions, used ATI's deburring tools to change the way their aluminum wheel-making customers manufacture their products. Wheel manufacturing uses both manual and machine processes. Removing flash material from the wheel castings is a tedious process that requires operators to manipulate heavy equipment by hand for several hours.
In addition, the soft alloy material and specifications for the finished product require a high level of accuracy. ATI has developed three types of deburring tools that provide the compliance necessary for safe, accurate finishing operations.
"iA-Robotics chose ATI's RC-300 radially-compliant deburring tools because they offered the type of product quality, compliant technology and support necessary for the process," says Saksit Suetrong, CEO and owner of iA-Robotics. "The environment is very harsh. There's contamination in the air. There's coolant, there's smog from the machining process. We've performed actual production tests utilizing the ATI deburring tool and it has proven to work in that environment."
Quality also has increased. The company didn't have to service any maintenance issues in the last eight months of its customers' production runs, Suetrong said in February.
Active vs. Passive Compliance
Advancements in robotic sensing technologies could lead to further improvements for the deburring process. In April, ATI introduced the Axia80 Force/Torque sensor. Force/Torque sensors enable active compliance. Most robotic deburring processes involve passive compliance. That means the robot and tool operate independently of each other. Compliance is engineered into the tools to handle different applications. But users can add a force/torque sensor to the robot for more precise, active compliance.
"The robot gets the information from the force sensor and makes modifications to its path, thus actively complying," Little explains. "It's measuring the force and reacting to the force."
Passive compliance tends to be less expensive but is not as precise as active compliance. As technology advances, robotics and robotic tooling technologies are becoming more affordable for manufacturers. According to Little, the aerospace industry has become a significant market for robotic material removal due to cost reduction.
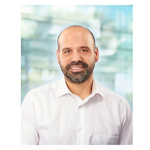
Jonathan Katz | Freelance Editor and Writer
Jonathan Katz, owner of JSK Communications, is a freelance writer with more than 15 years of experience in the publishing industry. He is the former managing editor for Cannabis Business Times and Cannabis Dispensary at GIE Media and a former managing editor of IndustryWeek magazine at Endeavor Business Media.
At IW, Katz covered a wide range of manufacturing topics, including automation, safety, facilities/plant operations and executive leadership.
Prior to freelancing, Katz served as a project manager for Content4Demand, a content marketing agency.