If you were to build a giant badass robot to pilot and needed a reason to fight worthy opponents, you'd need a good reason other than fulfilling your adolescent fantasies. Well, you wouldn't, but your investors, partners and employees probably will.
For MegaBots' co-founders—and co-pilots—Gui Cavalcanti and Matt Oehrlein, that reason is to inspire the next generation of roboticists to think big and build bigger. They want to demonstrate that anyone with enough know-how and determination can build one; you don't need a fancy innovation lab or bleeding edge tech.
Just about everything, except for the track base, was built at their Hayward, Calif. Base, called Fortress One. They used readily available equipment such as CNC machines and welding systems to fabricate the massive steel plates that would become their 16-ft., 12-ton Eagle Prime's sturdy husk.
Going up against a Japanese mech, their task is as daunting as an art competition against a Renaissance painter, so every gear, every joint, needs to be ready for war. But this is an extremely complex hydraulic robot filled with computers, actuators, and cameras, so its creators constantly tweaking and evolving the design.
To make matters more pressing, Cavalcanti and Oehrlein set a date for the fight, August 2017, and had several sponsors, thousands of Kickstarter contributors, and many more fans to appease.
Using traditional tooling means to perfect their first MK3-model robot would be too slow and expensive. Fortunately, Cavalcanti was already a rockstar in the robotics-heavy Boston area, having worked at Boston Dynamics, taught at Olin College, and co-founded Artisan's Asylum (a maker space in Somerville).
Not far from here, with only Harvard between them, sits Markforged, a high-strength 3D printer manufacturer where one of his former students, an applications engineer named Alex Crease, works.
In 2016, he reached out to Crease, who was more than willing to work with his former mentor, whose teaching style and enthusiasm eventually pushed him to start a 3D printing lab at Olin.
"Gui is a very inspirational person, because he's gets really excited about these obscure ideas and gets you really motivated to try them out," says Crease, who took his Principles of Engineering class three years ago.
Markforged, which usually services tooling, fixtures, and functional prototypes and parts for aerospace, automotive, and medical applications, provided the robotics startup with its Mark Two, fitting considering the previous MegaBot prototype was called the Mk. II.
The Mark Two 3D printer ($13,499) manufactures end-use parts out of durable materials including continuous carbon fiber, Kevlar, and Onyx, a chopped carbon fiber/ nylon plastic composite. The build volume is 320 mm x 132 mm x 154 mm, big enough to make the internal gears, sensor equipment, electronics housing, and functional protective casings MegaBots would needs.
"I love the versatility of the printer, and the way that the Eiger software allows me to reinforce parts selectively with fiber," Megabots engineer Lyra Levin says. "For parts where aesthetics matter, the matte black material and fantastic surface quality fits our look. For internal parts, the tolerance and fit is extremely good."
She estimates there are about 50 parts printed by the Mark Two in Eagle Prime, with 10 being unique. Levin is confident strength wasn't sacrificed for speed.
"I haven't done quantitative tests, but qualitatively, the Onyx parts are at least of the strength I would expect from machined aluminum, with extra stiffness – especially where reinforced by fiber," she says.
The most important aspect is that MegaBots makes these completely in house, not beholden a machine shop's schedule.
"There are a lot of things that can go wrong," Crease says of outsourcing production. "You can send a part out to be machined and it comes back and it's the wrong dimension. Then you have to wait another four to six weeks to get it re-machined, spending a few hundred to a few thousand more dollars."
Crease estimates using the Mark Two on average saves most customers 90% in time and costs compared to conventional machining.
Traditional manufacturers have also seen similar results.
"Our first Markforged printer paid itself off in less than 1.5 months and saved us over 81% versus machining," says Bill Hollingsworth, vice president of engineering at Dixon Valve.
The time savings for MegaBots may be even more important because the engineers can focus on applications relevant to the fight, such as the giant cannon arm's pneumatics or hydraulic response time, and not if the processing computer's brackets are the correct measurements.
Meanwhile, Markforged gets a chance to show off its printer's capabilities in one of the most highly anticipated engineering events of the century.
And to spread the same message all 3D printing companies have been telling.
"What we really aim to do is to bring down the barriers between getting an idea out the door and into a product," Crease says.
The fight ended up being pushed back a few weeks, now set for September— for logistical reasons, not because of Eagle Prime wasn't ready. When the fight is posted online shortly after, viewers will get to judge if regular folks fulfilling their big dreams is more than a folksy American cliché snuffed out by globalization, or the start of a new age of makers.
Even before the fight, MegaBots has already hooked Crease. He's currently working on a prototype he hopes will compete on BattleBots.
And who knows? Maybe in a few years, the student will face his teacher.
MegaBots has been very open about sharing its methods for creating these giant mechs, and plan on selling DIY kits for future members of its fighting league. Crease could presumably join the fray at some point, maybe even 3D print his whole bot.
If he does, he too will be fulfilling an adolescent fantasy, which when it comes to building things, even giant fighting robots, is something to celebrate, not scoff at.
"I see MegaBots less about the fighting and more about the inspiration," Crease says. "At its core MegaBots represents that anyone can make their wildest childhood dreams come true. BattleBots, Star Wars, and Legos fueled my engineering aspirations. I'm excited to see what the next generation of innovators will be able to do because of MegaBots."
Click HERE to return to the main MegaBots story.
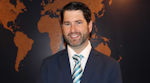
John Hitch | Editor, Fleet Maintenance
John Hitch, based out of Cleveland, Ohio, is the editor of Fleet Maintenance, a B2B magazine that addresses the service needs for all commercial vehicle makes and models (Classes 1-8), ranging from shop management strategies to the latest tools to enhance uptime.
He previously wrote about equipment and fleet operations and management for FleetOwner, and prior to that, manufacturing and advanced technology for IndustryWeek and New Equipment Digest. He is an award-winning journalist and former sonar technician aboard a nuclear-powered submarine where he served honorably aboard the fast-attack submarine USS Oklahoma City (SSN-723).