SLC: 2019 Toyota's Finding Success With Exoskeletons
As is the way of Toyota much study goes into anything new. And while that is usually applied to manufacturing production methods, it’s also applied to using technology as PPE.
“After extensive testing, this year we are now requiring the use of an exoskeleton as PPR at one of our plants in Indiana,” explained Marisol Barrero, Project Manage at Toyota Motor North America, at the Safety Leadership Conference.
Exoskeletons, which are body-worn devices for the purpose of reducing worker fatigue, have been used by Toyota team members at certain locations since 2015.
Barrero said the idea really took off at an industry meeting where automakers share best practices. “We are all very open about sharing ideas on safety and the use of technology to enhance safety. Our motto is there are no secrets on safety.”
By 2017 a few plants jumped on board with regard to testing on exoskeletons. In 2108 we started exoskeleton working groups from a few plants and then joined with educational institutions to formally study the impact.
In Nov. 2018, Kentucky was the first plant to require exoskeletons as PPE. The Indiana plant followed suit and by the end of 2019 across all plants.
In performing overhead work, company surveys showed that those who wore the exoskeletons reported a lower Rating of Perceived Discomfort (RPE).
An electromyography (EMG) study noted a statistically significant reduction of shoulder and back muscle maximum voluntary contraction (MVC), which translates to less muscle fatigue.
Based on these EMG studies s simple too was developed to systemically identify the processes that would benefit from upper body exoskeleton implementation.
So in November of 2018, a plant in Ontario, Canada became the first plant that required the use of exoskeletons for certain jobs. By the end of this year, it will be rolled out across all plants.
This deliberate process is why the program has been successful says, Barrero. “We didn’t just roll it out but instead involved our team members and studied the impact on workers.”
Why did the company choose to categorize its use as PPE? “We feel this best fits the paradigm and was an easy alignment with PPE already in place.”
The benefits of this technology for specific jobs at the company have been fewer injuries and lower costs. While the cost of the equipment can range from $3,000 to $70,000 it is much less compared to the toll of a shoulder injury on a team member.
Toyota is currently evaluating other technologies and their safety applications through its smart technology roadmap.
“Our success is due to a number of factors including a strong safety culture, and our enthusiastic safety leads at each plant that helps spread these technologies through the plant.”
Toyota is currently evaluating other technologies and their safety applications through its smart technology roadmap.
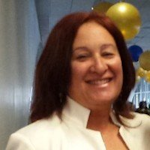
Adrienne Selko | Senior Editor - MH&L, IW, & EHS Today
Adrienne Selko has written about many topics over the 17 years she has been with Endeavor Business Media and currently focuses on workforce development strategies. Previously Adrienne was in corporate communications at a medical manufacturing company as well as a large regional bank.
She is the author of Do I Have to Wear Garlic Around My Neck? which made the Cleveland Plain Dealer's best sellers list. She is a senior editor at Material Handling & Logistics, EHS Today, and IndustryWeek.
Editorial Mission Statement:
Manufacturing is the enviable position of creating products, processes, and policies that solve the world’s problems. When the industry stepped up to manufacture what was necessary to combat the pandemic, it revealed its true nature. My goal is to showcase the sector’s ability to address a broad range of workforce issues including technology, training, diversity & inclusion, with a goal of enticing future generations to join this amazing sector.
Why I Find Manufacturing Interesting:
On my first day working for a company that made medical equipment such as MRIs, I toured the plant floor. On every wall was a photo of a person, mostly children. I asked my supervisor why this was the case and he said that the work we do at this company has saved these people’s lives. “We never forget how important our work is and everyone’s contribution to that.” From that moment on I was hooked on manufacturing.
I have talked with many people in this field who have transformed their own career development to assist others. For example, companies are hiring those with disabilities, those previously incarcerated, and other talent pools that have been underutilized. I have talked with leaders who have brought out the best in their workforce, as well as employees doing their best work while doing good for the world.