Calculating the Return on Investment of Laser Cleaning
The market for laser cleaning is growing rapidly, expanding by more than 10% from 2021 to 2022, and is forecast to grow by a third by 2028.
Manufacturers are increasingly turning to laser cleaning for several important reasons. Many of them find their current cleaning tech is too slow, damages metal substrates, or lacks precision. This results in more waste, rework, or poor performance.
Others are struggling to find workers for manual tasks and are automating the cleaning process. Some need to improve both speed and precision in manufacturing lines. At the same time, many manufacturers are concerned about using eco-friendly products and hitting sustainability goals.
Regardless of the reasons, companies are seeing significant ROIs from switching to laser cleaning technology in most cases. However, you may be asking yourself what is the return on investment and how you can quantify it.
In any equipment purchase, business managers want to know if and when their purchase will pay for itself and whether there is a substantive ROI that justifies the upfront expense.
Lower Maintenance and Operating Costs
If you are processing large batches of parts, operating costs can add up quickly. Laser cleaning systems can automate high-precision tasks at high speeds with minimal downtime.
Maintenance and operating costs can quickly turn production lines into money sinks. Estimating the total cost of operation (TCO) is important in assessing any equipment purchase, including:
- Prep time
- Power consumption
- Consumables
- Waste disposal
- Skilled man-hours
- Personal protective equipment is needed
- Changeover time and costs
- Training needed
- Maintenance required
For example, if you are using abrasive blasting machines, your production line is constantly interrupted. These machines destroy themselves over time due to the abrasives and require careful monitoring and maintenance for dust and sand accumulation, nozzle condition, cleaning, realignment for accuracy, and more. Manufacturers also have to manage tight tolerances for ablation thresholds to ensure cleaning without damaging the underlying substrate.
These are not issues with laser cleaning. Laser cleaning operates without consumables, can be fully automated, is energy efficient, and is 100% safe without requiring PPE or training when integrated with a class-1 laser safety enclosure. Further, because laser cleaning is a non-contact technology, the hardware can run for extended times without maintenance to keep production lines running longer, resulting in better throughput and performance.
Elimination of Manual Processes
One of the most expensive and variable line items for managers is the cost of labor. In today’s economic environment and challenging labor market, finding ways to manage labor costs and reduce manual tasks is essential to maintain margins. Automating processes may be the solution.
To begin with, you can approximate the ROI by comparing the cost of manual labor to the cost of the equipment. Automation may not be the winner in all cases, as labor is inexpensive in some companies.
There are other points you need to factor in. You need to consider whether eliminating manual tasks frees up personnel for other jobs. You also need to add in the potential increased production volume and the cost savings associated with laser cleaning.
Surface preparation frequently involves manual steps, but laser cleaning is made for automation and repeatability. With laser cleaning, you may be able to eliminate several of these steps, including:
- Manual Masking:
- Having to mask items with tape or other methods to prevent areas from being coated is time-consuming, labor-intensive, can limit production volume, and is inconsistent. Instead of masking a surface and then coating the part, laser cleaning allows you to coat the entire part and let the laser remove the coating from precise areas.
- Manual Cleaning:
- Many manufacturing processes require precise cleaning to protect sensitive areas from damage during the cleaning process. However, relying on manual cleaning can be tedious work, induce variability in your process, and result in errors and damage. Laser cleaning can automate this process due to its high precision in cleaning specific or sensitive areas without damage.
Prevention of Non-Quality Costs
A key metric for profitability is the cost of quality. It is not always easy to measure, but you know that poor quality can hurt your reputation and damage customer relationships. Scrap and rework are costly. In fact, many manufacturers find they have to limit production volume to avoid lowering quality.
Laser cleaning, however, significantly improves quality with highly accurate and repeatable processes. This provides a solid ROI and lowers non-quality costs by removing human and machine errors from the equation.
Lasers can help you meet high-performance requirements and industry standards. For example, it is used in battery manufacturing to clean areas before welding and meet the highest quality standards: manufacturers of lithium-ion battery cells target failure rates no higher than 1 in 10 million.
Capacity to Scale Production
Many manufacturers choose laser cleaning to scale up production volume. There are several reasons why laser systems are good at this task:
- Laser systems can clean surfaces at higher speeds than any other cleaning solution to reduce cleaning cycle time. Laser cleaning systems come at different power levels to adjust the cleaning speed, where a 200-watt laser can clean almost twice as fast as a 100-watt laser. Laser cleaning machines today can offer up to 3,000 watts of pulsed laser power.
- There's minimal mechanical movement required. As such, lasers can be directed and redirected rapidly. Using powerful galvo mirrors located inside the laser head, a laser can be adjusted on the fly in many cases—even if the part is incorrectly placed.
- Lasers are easy to automate. Their work surface is typically up to 300 x 300 millimeters (12 x 12 inches), so any work within this area can be handled through automation. Automatic focus compensation and part rotation can happen and, if the laser does need to be mechanically moved to process larger surfaces, this can be done using robots or gantry systems for linear head movements.
Because of the flexibility of laser cleaning, manufacturers can also minimize floor space usage, using fewer machines and increasing production capacity.
Long Operating Life
When buying a new machine, manufacturers expect it to run without anything going wrong. Problems are bound to happen, but the longer it takes and the fewer the problems, the better the ROI.
Fiber lasers are well known for their long operating life and high reliability. With a typical mean time between failures (MTBF) of 100,000 hours, they can often operate non-stop for more than 10 years with minimal maintenance and still offer the same high-quality results throughout that period.
By comparison, abrasive blasting machines require regular maintenance and replacement parts. The abrasive media used constantly wears down the machine and equipment, reducing the operating life. Dust collectors, pressure pots, blast nozzles, and hoses all wear out over time. Aggressive abrasives can reduce nozzle effectiveness to just 50 to 100 hours. Even glass beads may last just 200 hours before needing attention.
Each time there’s downtime for maintenance or replacement, you’re slowing down your production line to do it.
Fiber lasers keep your production line running longer. Even after you’ve shut down a particular line, fiber lasers can also be repurposed for other operations, even years after purchase.
A long operating life won’t provide a quick ROI, but it does lower your total cost of ownership.
Leveraging Green Subsidies
In the U.S., nearly half a billion dollars of government subsidies are available for switching to green and clean manufacturing technology. The Inflation Reduction Act of 2022 would create an additional $40 billion in clean manufacturing tax credits.
As a green technology, laser cleaning might give you access to government subsidies by reducing waste, energy usage, and harmful chemicals.
Laser cleaning replaces other polluting technologies that heavily rely on consumables such as chemical cleaning and sandblasting. Here are examples of common problems:
- Some chemical processes use strong products and require proper rinse water disposal to prevent contamination.
- With abrasive processes, the abrasive media gets mixed up with surface contaminants that are removed. Getting rid of this mixture in an environmentally friendly way can be complex and costly.
Manufacturers using laser systems do not have these concerns. Green benefits of laser cleaning include:
- No consumables
- No harmful chemicals
- Zero toxic waste generated
- Low-energy consumption
- Long operating life
Leveraging government subsidies can be a great way to shorten your payback and improve your ROI.
Conclusion
We hope that you found the tools needed to evaluate your application and understand if there’s a good business case for laser cleaning.
There are known cases where the ROI isn’t typically good. If you are refurbishing or reworking parts, laser cleaning may not provide a good ROI. For example, laser rust removal is rarely worth the investment because the volume is too low to get a reasonable payback.
Administrative procedures can also impact the ROI. In the medical or aerospace industries, there are complex processes when it comes to modifying any manufacturing process for safety concerns. Replacing a process—even an inefficient one—can turn into a long, complex, and expensive process. This alone may destroy the business case.
The best and fastest ROI tends to come from manufacturers that can eliminate manual masking and manual cleaning, and when cleaning the same type of parts in high-volume production.
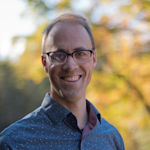
Guillaume Jobin | Application Specialist, Laserax
Trained as a Mechanical Engineer, Guillaume Jobin has more than 10 years of experience in automation and control. He is an Application Specialist at Laserax, where he analyzes clients' needs to design the right laser solutions for them. He is also a member of the Corporate Sustainability Committee.