Tight Shut-Off Applications: What to Look for in Valve Selection
Tight shut-off refers to the condition where there is no leakage of fluid when a valve is in the closed position. This is vital in flow systems where isolation is necessary between the upstream and the downstream. The isolation could be required as a safety measure or for maintenance activities to be carried out on downstream equipment. Shut-off valves are fitted into the flow systems to achieve this isolation.
There are many shut-off valves with unique characteristics and it's important to select the right valve for the intended tight shut-off application. Below are some of the factors to consider when selecting a valve for a tight shut-off application.
Valve Class
As defined by ANSI/FCI 70-2 2006, there are six leakage classifications for shut-off valves.
Class I: Valves in this class are also referred to as dust-tight valves and can include both metal and resilient seated valves. No actual tests are carried out to determine the leakage rate. They are similar in construction to class II to class IV valves.
Class II: These valves have metal-to-metal seats with a metallic piston ring seal. They can be constructed as balanced, single port, low seat load, or balanced, double port, high seat load.
Class III: They have a similar construction as class II valves. However, they also include medium-seat loaded valves.
Class IV: These are also referred to as metal-to-metal valves. They basically include balances and unbalanced single-port valves that have extra tight piston seals with metal-to-metal seats.
Class V: They have a similar construction as class IV valves; balanced, unbalanced, single port with low and high seat load.
Class VI: They are also known as soft seat valves designed for resilient sealing. Amongst the various classes, these are the most reliable for tight shut-off as the leakage allowed is much smaller than the other classes. These valves are tested with different test media and under different test pressures to determine the leakage rate. Class VI valves offer the best tight shut-off compared to other valve classes.
Valve Type
Though there are different types of valves (ball, butterfly, ball, gate, plug valve, etc.) for shut-off applications, each has its pros and cons, which must be considered during the selection process.
Butterfly valves are suitable for systems with clean fluids. Due to their disc sealing system, they are not suitable for fluids with slurries or grits. By design, when the disc is in the perpendicular position, the plate sits against the internal seal, creating a tight closure. They are more common in large-diameter pipes.
Gate valves by design can accommodate slurries and grits in the fluid, unlike butterfly valves.
Plug valves are quarter-turn style valves like butterfly valves. Plug valves are designed such that the rubber-encapsulated plug seats and the plug face are offset from the shaft centerline thus, providing a tight seal when closed. Though similar to ball valves, plug valves have no cavities that might trap media/fluid in any position.
Pinch valves, also known as clamp valves, are designed to shut off the flow from abrasive, granular, fibrous, or corrosive media optimally. The rubber sleeve in the clamp valve has the capability to trap the particles around it, resulting in an excellent shut-off.
Type of Actuation
A valve can be actuated by different mechanisms. They are manual, electrical, pneumatic, and hydraulic actuators.
Manual actuation is operated by hand. In simple flow systems, this is economical. However, in high-pressure flow systems, hydraulic actuators are capable of generating high power to shut off the flow.
Pneumatic actuators are generally quicker than hydraulic ones but still provide comparable actuation power much more than electrically energized actuators. Pneumatic actuation may be powered by compact air cylinders.
Shut-off valves should be selected with the intended actuation in mind to ensure optimum compatibility.
Valve Seat Type
Valve seats refer to the closure members that are in contact with each other during the closure of the valve. The seat materials are subject to wear and tear during the valve-closing process. There are two types of valve seats; metal seating and soft seating.
Soft seating uses soft materials such as rubber or plastic on one or both of the closure surfaces. These materials are easy to match and can achieve a high degree of fluid tightness repeatedly without considerable wear.
Metal seats tend to wear off over time with repeated open and close movements of the valve.
Valve Material
There are different materials for the different components in a valve, ranging from the housing to the seating material. Materials commonly used in valves include aluminum, copper, bronze, brass, iron, carbon steel, stainless steel, etc.
Stainless steels offer excellent resistance to corrosion and stress cracking.
Aluminum has extremely high corrosion resistance, but it is reactive to other metals.
Plastics are lightweight but have less strength than metals. It's vital that the ambient condition for application is properly assessed to determine the best material for the valve.
Fluid Type
A flow system could contain different fluids such as liquids, gases, or even slurry. In addition, the type of fluid could be corrosive or non-corrosive. For combustible gaseous systems, gas ball valves are much better than standard ball valves. They offer better shut-off and sealing than conventional ones. Their quick open and close movement makes them ideal for preventing backflows and even contamination.
Shut-off valves with an element directly in the flow path, such as butterfly and globe valves, will wear off in slurry applications. Ball valves remain one of the most reliable shut-off valves in liquid flow systems.
Conclusion
Choosing the right valve does not end in selecting the valve type. It also considers the component materials, class of valve, the fluid type, and the operating conditions. There are different valves for different industrial applications. There is a need to understand the tight shut-off requirements of the flow system before selecting a shut-off valve.
About the Author
Gilbert Welsford Jr.
Gilbert Welsford is a highly regarded expert in the valve industry, known for his engineering excellence and extensive experience. In 2011, Gilbert founded ValveMan.com, an online platform specializing in valves and valve-related products. Gilbert has played a pivotal role in the design, manufacturing, and application of various valve types. His expertise encompasses control valves, ball valves, globe valves, butterfly valves, check valves, and more enabling him to provide tailored solutions to meet diverse industry needs.
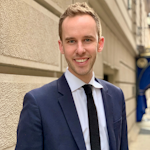
Gilbert Welsford Jr.
Gilbert Welsford is a highly regarded expert in the valve industry, known for his engineering excellence and extensive experience. As the third-generation owner of the FS Welsford Company, the parent company of ValveMan.com, Gilbert has built upon a rich family legacy in the industry.
In 2011, Gilbert founded ValveMan.com, a leading online platform specializing in valves and valve-related products. Under his leadership, ValveMan has grown into a trusted resource for valve engineers and buyers, offering a wide range of high-quality valves and exceptional customer service.
With a profound understanding of fluid dynamics and precision engineering, Gilbert has played a pivotal role in the design, manufacturing, and application of various valve types. His expertise encompasses control valves, ball valves, globe valves, butterfly valves, check valves, and more enabling him to provide tailored solutions to meet diverse industry needs.
Gilbert's collaborative approach and exceptional communication skills have fostered strong relationships with clients across multiple sectors, including oil and gas, petrochemicals, power generation, water treatment, and manufacturing. His ability to analyze complex valve systems and offer expert guidance has consistently resulted in successful project outcomes.
Driven by his passion for innovation and commitment to excellence, Gilbert remains at the forefront of the valve industry. By staying informed about the latest advancements and industry trends, he continues to deliver cutting-edge valve solutions that exceed customer expectations.