Automated Material Handling: Resistance is Futile (and Unnecessary)
Back when Brian McNamara started working at Southworth Products in 1981, the material handling equipment maker's current president and CEO saw the beginnings of a brave, new automated world on the factory floor. Sure, there weren't artificially intelligent self-driving lift trucks delivering pallets to collaborative robots, but there were AGVs chugging along magnetic tape pathways and welding robots.
And the pressure to increase automation was also no different. In regards to material handling, "How much?" was, is, and probably will be for a long time the question needing an answer.
First off, realize that question can be partially answered. You can go semi-automatic, and still have enough firepower to stay competitive.
"We get lost in if we automate or we don't," McNamara says. "It's not black or white."
That gray area is how the Maine-based manufacturer has stayed relevant in a world of servos, semiconductors, and artificial intelligence despite engineering with springs, steel, and hydraulics.
Ergonomics has been the company mission since the Nixonian era. As industry incrementally became smarter and faster every year, Southworth developed more and more products to help humans move heavy things easier, you know, without needing to scarf down Motrin all weekend to recover. The PalletPal in 1989 was a standout that used simple mechanisms and springs to keep boxes at an optimal height so you wouldn’t need to constantly bend over.
And while you are deciding how much to automate, you can optimize your assembly line so that it's suitable for your robots and nearly obsolete humans.
"If you pre-set assemblies just as if a robot would interface with it to do the welding, and put a human worker there, his efficiency is going to go up dramatically," McNamara advises.
Surprisingly, McNamara, whose company focuses squarely on ergonomics, a very human concern, thinks his customer base should do their best to implement robots in as many material handling applications as possible.
"From where we stand, automation should be the goal for everybody," McNamara says. "There is a consistency, predictability, and efficiency to automation that should be a high priority for everyone."
He's not wrong; adopting automation is inevitable. But for him to say it?
Southworth does sell plenty of lift tables, which can be used as the Z-axis in many automated applications, but McNamara says Southworth's mission of efficiency and ergonomics would ring hollow if he didn’t advocate for automation.
"If people just sit on their hands, they're absolutely setting themselves up to be left behind," the CEO warns.
You can check our directory to see just how advanced material handling is becoming, from self-driving lift trucks to robot pickers with humanlike dexterity. The 24/7 factory dreamed about in the early '80s is now a reality for some (though no one called it that because that term hadn't been coined yet).
However, it will be a long time before every plant and factory completely automates. Along with increased efficiency and productivity, going robo has its costs.
”Automation brings with it high-end investment, and there are situation concerns about servicing it, and technical requirements," McNamara says. "There is also some concern about flexibility."
The biggest hurdle to mass adoption, though, as pointed out by the 2016 MHI Annual Industry Report, was "lack of a clear business case," which rose from 36% to 43% from 2015.
"Warehouse A decides to automate, but warehouse B can’t see it itself as being identical," McNamara explains.
Instead of keeping up with the Joneses, that second warehouse lets the early adopters try it out and wait until it is sure automation will provide a clear benefit.
The survey says other barriers include: “lack of adequate talent to use technologies effectively” (38%) and "cultural aversion to risk” (35%)."
This can all be summed up as a lack of confidence, McNamara says.
"People have a hard time putting their product into a system they might have seen in a magazine or on the Internet, and know with confidence that it's going to work," explains McNamara, recalling what many customers tell him. "And if something goes wrong, they want to know it can keep it running."
But are there any lessons to be learned from the early 1980s, when American automakers failed to automate and fell behind Japan, which embraced it? Shouldn't everyone be scheduling integrators right now so they won't fall behind?
"That's been a difficult message to get across," McNamara says. "It is such a massive investment. Do they think it will work? Do they think they'll get an ROI? That's where the challenges come in."
There are some serious barriers, and the MHI Report offers some key strategies to address them:
- Be measured when considering robotics and automation. Challenge engineers to be clear in their vision for deploying robotics within an operation. Determine ROI and make sure you develop a clear understanding of where and when automation investments make sense for your business.
- Go slow initially in implementing robotics and automation. Consider starting with a semi-automated design to learn and understand how far to take robotics. Often, the most effective answer may be several steps short of a completely lights-out operation.
- Talk to companies using the technology. When working with vendors, ask to speak with their existing customers and tour facilities where the technology has already been implemented. Many companies are very open about sharing their experiences and lessons learned.
For his part, McNamara says Southworth has automated some of its manufacturing to the point where "if we shut down, we have a very difficult time working around it."
And while he loves the consistency of robotic welders, the lower volume and more customized approach of Southworth doesn't justify larger-scale automation.
And that's possibly the real lesson here. Just because you see a new automated forklift that dispenses espresso and gives you back rubs come out doesn't mean your widget factory needs to blow your Q4 profits on a down payment for one. Find out what will work for you, and make progress to make it work.
"Not all of us are going to get to go to Tahiti, but there are a whole lot of other vacations that are good for our bodies and good for our minds," McNamara offers. "To me, automation is like Tahiti. Yeah, we'd all love to get there, but if there are reasons we can't, you don’t just wait and not take time off."
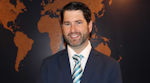
John Hitch | Editor, Fleet Maintenance
John Hitch, based out of Cleveland, Ohio, is the editor of Fleet Maintenance, a B2B magazine that addresses the service needs for all commercial vehicle makes and models (Classes 1-8), ranging from shop management strategies to the latest tools to enhance uptime.
He previously wrote about equipment and fleet operations and management for FleetOwner, and prior to that, manufacturing and advanced technology for IndustryWeek and New Equipment Digest. He is an award-winning journalist and former sonar technician aboard a nuclear-powered submarine where he served honorably aboard the fast-attack submarine USS Oklahoma City (SSN-723).